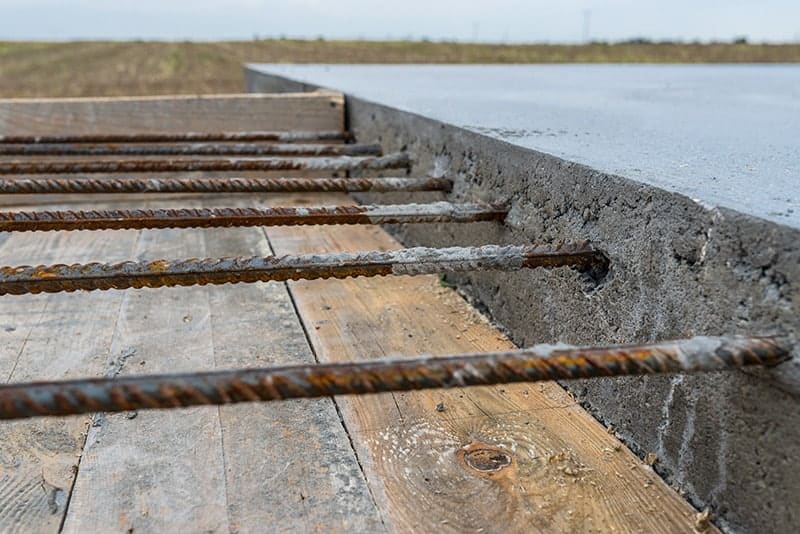
Korodowanie to niepożądany proces, który prowadzi do niszczenia materiałów. Chociaż najczęściej kojarzony jest z metalami, to jednak dotyczy także betonu, drewna czy tworzyw sztucznych. Co powoduje korozję? Jak zapobiegać korozji? Co zrobić, gdy już korozja się pojawi? Sprawdź nasz poradnik, w którym znajdziesz najważniejsze informacje na temat korozji!
Spis treści:
Co to jest korozja?
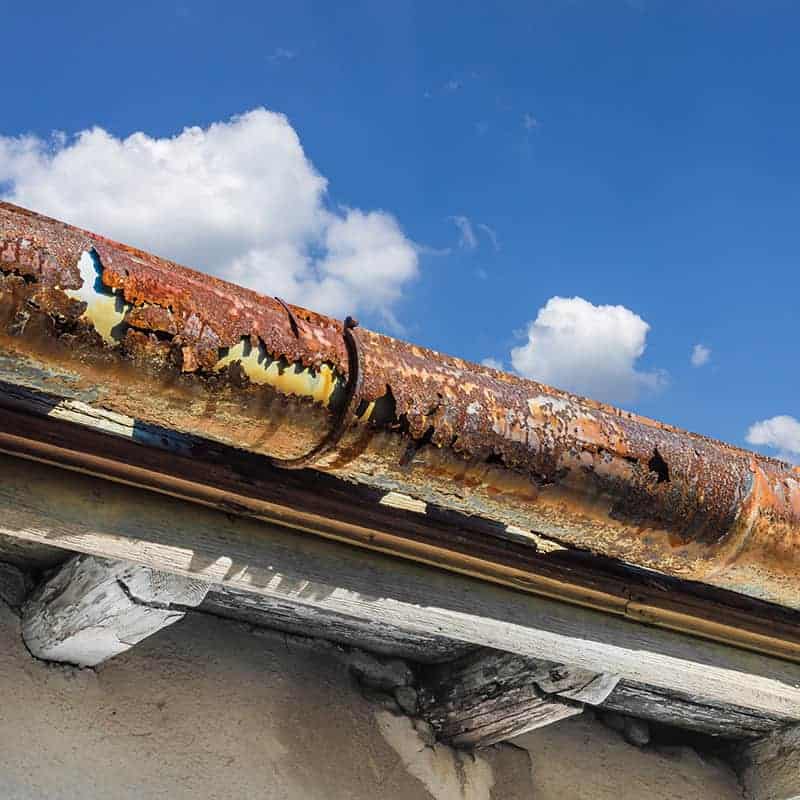
Proces określany jako korozja (od łacińskiego „corrosio”, co tłumaczone jest jako „zżeranie”) to proces stopniowego niszczenia powierzchni metalu, które pojawia się na skutek ich reakcji z otoczeniem. Korodujące materiały zmieniają swoją strukturę. Początkowo ich powierzchnia ma pierwotny wygląd i właściwości, a następnie na skutek korozji dochodzi do zniszczeń na powierzchni metalu. Proces stopniowego niszczenia metali może stwarzać duże niebezpieczeństwo. Korozja metali jest także określana jako rdzewienie żelaza – proces ten dotyczy wtedy materiałów metalowych, na których pojawia się charakterystyczny, rudawy nalot, czyli rdza. Obecnie korozja uznawana jest za jeden z najbardziej szkodliwych czynników dla materiałów konstrukcyjnych. Aby zapobiegać korozji, stosuje się obecnie szereg technik, które pozwalają na zredukowanie ryzyka pojawiania się ognisk korozji. Odpowiednio dobrane zmniejszają ryzyko korozji i jednocześnie chronią infrastrukturę, produkty czy części przed ich poważnym uszkodzeniem, a przez to zwiększają bezpieczeństwo użytkowania konstrukcji stalowych narażonych na niszczenie. W tym artykule skoncentrujemy się na procesie rdzewienia metali, ponieważ występuje on najczęściej i to właśnie korozja metalu jest powodem licznych problemów, z jakimi boryka się zarówno przemysł, jak i osoby indywidualne – właściciele domów, mieszkań, działek, samochodów.
Rodzaje korozji metalu
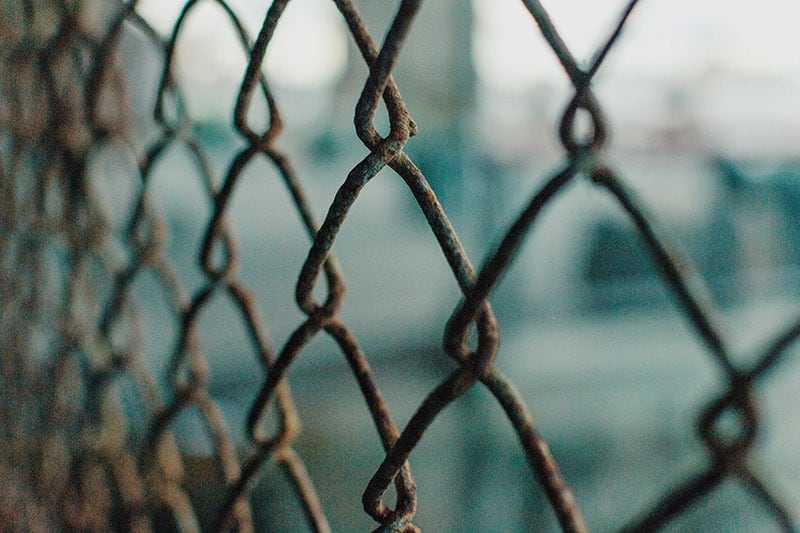
Do pojawienia się korozji metalu dochodzi na skutek wystawienia powierzchni metalu na czynniki zewnętrzne. Rodzaj korozji jest zależny wtedy od tego, z jakimi czynnikami styka się metal. Wyróżnia się 4 główne typy korozji metalu:
- Korozja elektrochemiczna,
- Korozja chemiczna,
- Korozja mikrobiologiczna,
- Korozja fizyczna.
Korozja elektrochemiczna | W przypadku metali główną przyczyną ich niszczenia jest korozja elektrochemiczna. Korozja elektrochemiczna zachodzi głównie na skutek stykania się metalu z wodą, ziemią albo wilgotnymi gazami zawartymi w powietrzu. Elektrochemiczna korozja prowadzi do utleniania się powierzchni metali i powstawania na powierzchni metali rdzy lub innych nalotów. |
Korozja chemiczna | Drugą przyczyną uszkadzania metali jest korozja chemiczna. Korozja chemiczna zachodzi w warunkach suchych. Korozja chemiczna zachodzi przy stykaniu się metalu z gazami i cieczami, które nie przewodzą prądu. |
Korozja mikrobiologiczna | Do korozji mikrobiologicznej dochodzi na skutek działania czynników biologicznych, na przykład stykania się materiału z bakteriami i grzybami. Na korozję mikrobiologiczną najczęściej narażone jest drewno. |
Korozja fizyczna | Korozja fizyczna pojawia się wtedy, gdy materiał jest narażony na czynniki fizyczne, na przykład na wysokie i niskie temperatury, topnienie, promieniowanie, podwyższone pole elektryczne, naprężenia powstające przy nadmiernym obciążeniu, ale też uszkodzenia mechaniczne. Czynniki fizyczne także powodują przyspieszenie procesów korozji elektrochemicznej, chemicznej oraz mikrobiologicznej. |
Co powoduje korozję
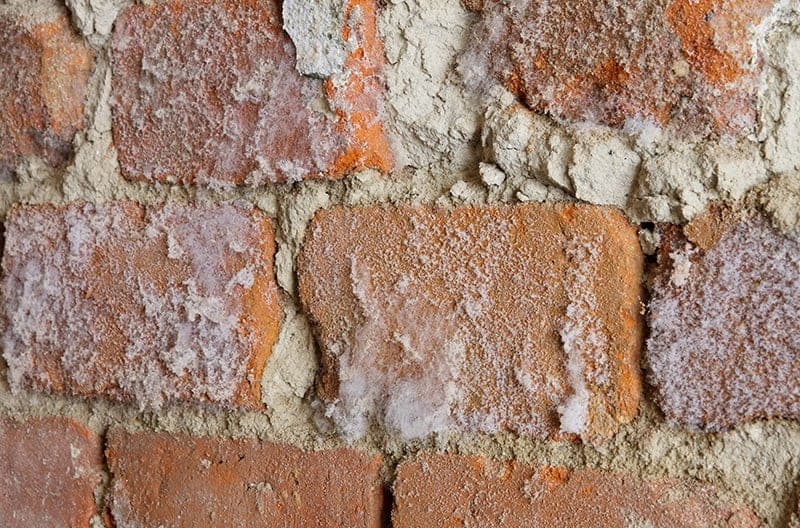
Korozja metali może mieć różne rodzaje w zależności od tego, jakie czynniki sprzyjają powstawaniu korozji. Jakie czynniki najczęściej powodują więc pojawienie się niszczenie powierzchni metalu? Wśród czynników, które najczęściej wywołują korozję, znajdują się:
- Wysoka wilgotność powietrza,
- Wilgoć powierzchniowa,
- Opady deszczu, opady śniegu,
- Sól – także w słonej wodzie morskiej,
- Kontakt metalu z glebą,
- Skrajnie niskie i wysokie temperatury – także powstałe podczas spawania,
- Kwas i zasady,
- Zakwaszone wody – solne, siarkowe,
- Kontakt metalu z innymi materiałami, na przykład metalami, betonem,
- Smary przemysłowe.
Dokładny podział środowisk korozyjnych można znaleźć w normie PN-EN ISO 12944-2 (Farby i lakiery. Ochrona konstrukcji stalowych za pomocą ochronnych systemów malarskich. Część 2: Klasyfikacja środowisk). Wyróżnia ona 5 różnych środowisk oznaczonych symbolami C1, C2, C3, C4 oraz C5. Środowisko C1 jest najmniej zagrażające, natomiast C5 najbardziej. Zatem elektrochemiczna korozja metali może powstać na skutek kontaktu z różnymi czynnikami zewnętrznymi występującymi w wielu środowiskach. Stąd korozja stanowi również tak duże ryzyko dla wszelkiego rodzaju konstrukcji, maszyn, urządzeń, części.
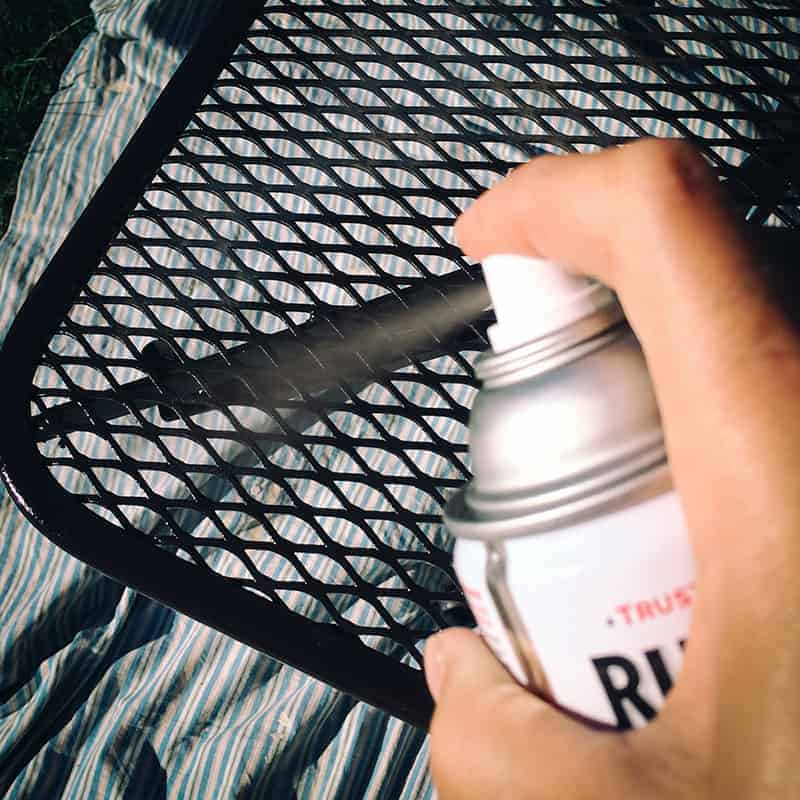
Proces korozji, chociaż kojarzony jest z metalami, w rzeczywistości dotyczy także innych typów materiałów, które są podatne na uszkodzenie na skutek kontaktu z czynnikami zewnętrznymi.
Na korozję narażone są poniższe rodzaje materiałów:
- Metale oraz ich stopy, na przykład żelazo i jego stopy jak stal, stopy aluminium,
- Beton i żelbet,
- Drewno,
- Szkło,
- Skały,
- Tworzywa sztuczne.
Aby doszło do korozji metali, konieczne jest powstanie sprzyjających jej warunków. Na utlenianie najbardziej narażone są te materiały, które:
- Wystawione są na szereg czynników sprzyjających korozji, na przykład:
- czynniki pogodowe,
- naprężenia,
- uszkodzenia mechaniczne,
- wysokie i niskie temperatury.
- Nie zostały odpowiednio zabezpieczone przed czynnikami powodującymi korodowanie.
- Są wystawione na silne działanie czynników – wówczas nawet odpowiednio dobrane zabezpieczenia antykorozyjne z czasem przestają pełnić swoją funkcję, dlatego konieczna jest ich odnowa.
Jak wygląda korozja?
Korozja może mieć zróżnicowany wygląd, dlatego warto wiedzieć, w jaki sposób ją rozpoznać, aby można było szybko zareagować i ją usunąć. W przypadku metali korozji często towarzyszy rdza, czyli rudawy nalot, który może z czasem zmieniać się w proszek. Powstaje on na skutek procesu utleniania żelaza i jego stopów, na przykład stali. Gdy dojdzie do zaawansowanej korozji, cały przedmiot może ulec przemianie w rdzę i rozpadowi. Korozja pozostałych typów metali wygląda inaczej. Przykładowo korozja aluminium powstaje kiedy metal jakim jest glin kontaktuje się z innymi metalami, na przykład cynkiem, miedzią, wybranymi rodzajami stali, a także betonem. Na aluminium pojawiają się wtedy jaśniejsze albo brązowawe wykwity korozji. Wyróżnia się różne typy korozji pod kątem wyglądu zniszczeń:
Korozja ogólna | Ta korozja rozwija się na całej powierzchni metalu i ma formę równomiernego nalotu, może powodować powstanie rozwarstwień. |
Korozja wżerowa | Ta korozja tworzy wąskie i głębokie otwory, które penetrują do wewnątrz materiału, natomiast jego pozostała powierzchnia pozostaje nienaruszona. |
Korozja szczelinowa | Ta korozja powstaje w szczelinach, w których dochodzi do nadmiernego nagromadzenia czynników sprzyjających korozji, na przykład w narożnikach, kieszeniach. |
Korozja międzykrystaliczna | Ta korozja pojawia się w miejscach, gdzie metal ma ziarnistą strukturę i wywołuje uszkodzenia punktowe. |
Jeżeli na powierzchni można zauważyć ogniska korozji, wtedy jest to znak, że metal wymaga odpowiedniej konserwacji. Brak reakcji spowoduje dalsze postępowanie procesu niszczenia metalu, który może spowodować jego zniszczenie i duże straty.
Dlaczego korozja jest niebezpieczna?
Korodowanie jest procesem niepożądanym, który może spowodować poważne straty bezpośrednie i pośrednie. Bezpośrednie straty odnoszą się do kosztów zniszczonych przez rdzę materiałów oraz kosztów zabezpieczania konstrukcji przed procesami korodowania metali. Szacuje się, że straty te wynoszą biliony dolarów rocznie – w skali globalnej na rok niszczeje nawet około 25 milionów ton stali. Według przeprowadzonego w 2010 roku badania w Polsce korozja spowodowała straty wynoszące 100 miliardów złotych. Poza stratami bezpośrednimi korozja powoduje także straty pośrednie, które odnoszą się do zagrożenia życia i zdrowia ludzi oraz zagrożenia dla środowiska naturalnego.
Korozja była jednym z czynników, który spowodował katastrofę mostu wiszącego Silver Bridge w USA w 1967 roku, w którym zginęło 46 osób. Korozja przyczyniła się także do zniszczeń na moście Kinzua w USA w 2003 roku, który został uszkodzony podczas tornada, ponieważ korozji uległ metal śrub.
Pod kątem zagrożenia dla środowiska naturalnego rdzewienie żelaza jest między innymi przyczyną uszkodzeń rurociągów oraz zbiorników przechowujących produkty naftowe oraz inne szkodliwe dla natury substancje.
Współczesna nauka zna stopy metali, które są w wysokim stopniu odporne na korodowanie. Określane są one jako CRA – corrosion resistant alloys, co tłumaczone jest jako stopy odporne na utlenianie.
CRA cechują się długotrwałą odpornością na czynniki zewnętrzne powodujące korodowanie i są one używane w tych środowiskach, gdzie szybkość korozji jest duża i stanowi ona szczególne niebezpieczeństwo. Stosowane są one między innymi w branży gazowej i w produkcji ropy naftowej, a ponadto w branżach:
- gastronomicznej,
- medycznej,
- chemicznej,
- farmaceutycznej,
- kosmetycznej,
- motoryzacyjnej.
Najbardziej popularnym materiałem odpornym na rdzewienie jest stal nierdzewna, która określana jest także jako INOX (od francuskiego „inoxydable”, co tłumaczone jest jako „nieutleniający się”). Nierdzewność jest wynikiem odpowiednich dodatków stopowych, głównie chromu. W stali nierdzewnej minimalna zawartość chromu to 11%. Najczęściej spotykane stropy mają 18% chromu oraz 10% niklu i określane są jako stal 18/10.
Do stopów odpornych zaliczane są między innymi poniższe gatunki:
- Stop 316L – stal nierdzewna austenityczna,
- Stop Alloy 22 – stop niklowo-chromowo-molibdenowy,
- Stop Alloy 601 – zawierający nikiel, chrom, żelazo i glin,
- Stop ZERON 100 – stop stali nierdzewnej zawierający chrom, nikiel i molibden.
Warto pamiętać o tym, że stal nierdzewna nie zagwarantuje całkowitej odporności na rdzewienie. Gdy jest wystawiona na działanie silnych czynników wywołujących utlenianie lub zostanie uszkodzona mechanicznie, może pojawić się na niej rdza.
Czy aluminium jest antykorozyjne?
Bardzo często można spotkać się z przekonaniem, że antykorozyjne właściwości ma aluminium. W tym przypadku rzeczywiście nie dochodzi do korozji w tak wysokim stopniu, ale nie oznacza to całkowitej oporności tego metalu. Warto zaznaczyć, że ten metal narażony jest na korozję kontaktową, galwaniczną, która wywołana jest przez kontakt z określonymi powierzchniami:
- betonem,
- miedzią,
- cynkiem,
- wybranymi rodzajami stali.
Właśnie dlatego przy montażu elementów aluminiowych duże znaczenie ma ich otoczenie. Dodatkowo do korozji może dojść na skutek używania go w mokrym i zasolonym środowisku, na przykład w środowisku morskim, a także na skutek kontaktu z silnymi kwasami i zasadami.
Jak zapobiegać korozji?
Zapobieganie korozji jest bardzo ważne, ponieważ można wtedy znacznie opóźnić jej występowanie lub też całkowicie ją wyeliminować. Aktualnie do dyspozycji jest wiele sposobów zapobiegania i ograniczenia występowania korozji. Co zastosować aby korozja materiałów się nie pojawiła?
Odpowiedni dobór materiałów | Zależnie od środowiska, w którym mają się one znajdować |
Dopasowanie materiałów | Duże znaczenie ma również dobranie materiałów tak, aby wyeliminować ich niekompatybilność, która może spowodować powstanie korozji. |
Stosowanie powłok ochronnych | Właściwie dobrane powłoki antykorozyjne pozwalają na zmniejszenie ryzyka korozji. Obecnie stosowane są różne rodzaje powłok, które prezentujemy w dalszej części naszego artykułu. |
Zarządzanie korozją | Systematyczne monitorowanie powierzchni w celu przeciwdziałania i szybkiego wykrywania korozji. |
Konserwacja | Systematyczna konserwacja pozwala na zredukowanie ryzyka związanego z powstaniem korozji. Jej zaniechanie może spowodować pojawienie się ognisk rdzy i nalotów zwłaszcza w środowiskach zewnętrznych. |
Techniki antykorozyjne
Najlepszym sposobem zapobiegania rdzewieniu są antykorozyjne techniki przemysłowe, które pozwalają na uzyskanie optymalnego stopnia ochrony metali przed czynnikami zewnętrznymi. Ochrona metali przed korozją jest prowadzona zarówno na etapie projektowania i produkcji, jak i eksploatacji.
- Cynkowanie. Cynkowanie zaliczane jest do najczęściej prowadzonych metod ochrony metali przed korodowaniem. Podczas procesu cynkowania dochodzi do pokrycia elementów stalowych ściśle przylegającą do nich warstwą cynku. Powłoka cynkowa chroni przed korozją wywołaną na skutek działania wody i powietrza. Właściwie wykonana powłoka cynkowa chroni przed korodowaniem – elementy cynkowane są nawet kilkanaście razy bardziej odporne na niekorzystne procesy korozyjne od nieocynkowanych. Co ważne, cynkowanie chroni nie tylko wtedy, gdy powłoka cynkowa jest szczelna, ale także wtedy, gdy dochodzi do jej naruszenia na bazie zjawiska ochrony katodowej. Po wykonaniu cynkowania na przedmiocie pojawia się charakterystyczna, srebrzysta powłoka cynkowa. Zapobieganie rdzewieniu poprzez cynkowanie jest procesem prowadzonym w firmach nazywanych cynkowniami albo ocynkowniami. Walka z korozją poprzez cynkowanie może być prowadzone kilkoma metodami:
- Cynkowanie proszkowe – to metoda polegająca na umieszczeniu przedmiotu w sproszkowanym cynku z dodatkiem tlenku cynku i poddaniu go działaniu wysokiej temperatury na poziomie 350–400 °C na kilka godzin.
- Cynkowanie galwaniczne – jest to metoda elektrolitycznego zabezpieczania metali przed korozją, która wykorzystuje do tego celu prąd elektryczny i substancje pochodzące z elektrolitów. Przedmiot umieszczany jest w kąpieli galwanicznej i poddawany działaniu prądu pomiędzy elektrodami.
- Cynkowanie ogniowe, inaczej cynkowanie zanurzeniowe, na przykład proces Sendzimira – przedmiot zanurzany jest w kąpieli cynkowej, czyli w płynnym cynku w temperaturze około 440-460 °C. Dochodzi wtedy do wytworzenia warstwy cynku, która ma postać stopu cynku i żelaza.
- Cynkowanie natryskowe – proces polegający na natryskiwaniu powłoki cynkowej na przedmiot. Używany jest on głównie wtedy, gdy konieczne jest ocynkowanie przedmiotów o dużych gabarytach. Powłoka cynkowa może być tym sposobem nanoszona na materiały, które nie mogą być wystawione na działanie wysokich temperatur.
- Malowanie proszkowe. Malowanie proszkowe, które określane jest jako lakierowanie proszkowe, łączy w sobie dwie korzyści – pozwala na zabezpieczenie przedmiotów przed korozją i nadaje im atrakcyjny wygląd. Proces malowania proszkowego polega na wykorzystaniu naelektryzowanych cząsteczek farby proszkowej, które mają wielkość 20-100 mikrometrów. Cząsteczki farby nakładane są na metal i utrzymują się na nim z wykorzystaniem sił elektrostatycznych, a następnie poddawane są nagrzewaniu w wysokich temperaturach 140-200 °C, co prowadzi do ich polimeryzacji i stworzenia trwałej powłoki lakierniczej metalu. Lakierowanie proszkowe bardzo często prowadzone jest na elementach już ocynkowanych, co zapewnia dodatkową ochronę przed korodowaniem matali. Technika lakierowania proszkowego związana jest z wieloma zaletami, dlatego dzisiaj używana jest bardzo często. Nie tylko skutecznie ogranicza niekorzystne procesy korozyjne na powierzchnią metalu, ale również jest przyjazna dla środowiska naturalnego, umożliwia uzyskanie powłok ochronnych, które pozwalają na zamaskowanie niedokładnej obróbki, a także pozwala na nadanie powierzchni metali różnorodnych kolorów. Procesem malowania (lakierowania) proszkowego zajmują się firmy określane jako lakiernie proszkowe. Stosowane są dwie główne techniki malowania proszkowego:
- Natrysk elektrostatyczny – określany także jako metoda wysokonapięciowa lub „korona”,
- Natrysk elektrokinetyczny – z wykorzystaniem metody tarciowej triboelektryzacji, w skrócie „tribo”.
- Farby antykorozyjne. Trzecia technika ochrony materiałów przed korozją, która używana jest zarówno przemysłowo, jak i indywidualnie, to malowanie farbami antykorozyjnymi. Farba antykorozyjna nanoszona jest na powierzchnią metalu ręcznie lub za pomocą urządzeń do malowania natryskowego. Na rynku znajduje się szeroka gama farb antykorozyjnych, które pozwalają na uzyskanie bardzo dobrych efektów w ochronie przed korozją elektrochemiczną. Duże znaczenie ma jednak prawidłowy dobór farby oraz jej właściwe nałożenie – jakiekolwiek błędy mogą spowodować pojawienie się ryzyka korozji elektrochemicznej. Więcej informacji dotyczących farb antykorozyjnych prezentujemy w dalszej części artykułu.
Środki zabezpieczające przed rdzą
Korozja i sposoby jej zapobiegania w domu – do samodzielnego zabezpieczenia powierzchni metalowych przed rdzą można wykorzystać różnego rodzaju preparaty. Kiedy je stosować i jaką ochronę wybrać na metal?
W warunkach domowych preparaty zabezpieczające używane są między innymi na:
- Ogrodzenia,
- Balustrady,
- Barierki,
- Bramy,
- Słupki,
- Konstrukcje ogrodowe,
- Garaże,
- Wiaty,
- Drzwi,
- Meble,
- Rury,
- Grzejniki,
- Elementy pojazdów,
- Zbiorniki,
- Zadaszenia.
Wśród dostępnych produktów znajduje się kilka ich typów, które różnią się pod względem swoich właściwości oraz sposobu stosowania:
Farba antykorozyjna
Często do użytku domowego stosowane są farby antykorozyjne, które ze względu na swój skład mogą zabezpieczyć powierzchnie metalowe przed rdzewieniem i poprawić ich estetykę.
Rodzaje farb antykorozyjnych stosowanych na metal:
- Farby akrylowe – zawierają w składzie żywice akrylowe, dlatego są odporne na warunki atmosferyczne. Mają niskie ceny, dlatego są najlepsze do niewymagających zastosowań. Nadają się do powierzchni stali ocynkowanej, powierzchni miedzi, aluminium.
- Farby chlorokauczukowe – sprawdzają się na zewnątrz i wewnątrz, poza środowiskiem agresywnym chemicznie. Stosowane głównie na powierzchnie stalowe i na żelazo.
- Farby alkidowe – stosowane do metali na zewnątrz i we wnętrzach, w umiarkowanych warunkach sprzyjających korozji.
- Farby poliuretanowe i uretanowe – wysoce odporne na czynniki chemiczne i na wilgoć. Wyróżniają się elastycznością i odpornością powierzchni na ścieranie.
- Farby poliwinylowe – używane do stali ocynkowanej, mogą być używane na zewnątrz.
- Farby żaroodporne – stosowane do powierzchni nagrzewających się do wysokich temperatur, na przykład grzejników, kominków, grillów.
Dostępne są także farby z mieszanymi składnikami, na przykład alkidowo-akrylowa, alkidowo-uretanowa.
Farby antykorozyjne są sprzedawane w wielu kolorach do wyboru, co powoduje, że mogą one jednocześnie ochronić powierzchnię przed korozją i nadać jej atrakcyjny wygląd. Oferowane są w różnych wariantach wykończenia powierzchni:
- matowe,
- połyskowe,
- z efektem metalicznym,
- z efektem młotkowym.
Pod względem formy farby antykorozyjne są oferowane w puszkach oraz w sprayach. Mogą być nakładane pędzlem, wałkiem, metodą natryskową.
Odrdzewiacz – neutralizator rdzy
Środki używane do usuwania istniejącej rdzy oraz jako preparaty gruntujące i antykorozyjne. Mogą być używane pod powłoki z farb antykorozyjnych. Zawierają żywice epoksydowe. Często dostępne są w formie praktycznych sprayów, które pozwalają na naniesienie środka bezpośrednio na metal.
Grunt i podkład antykorozyjny
Preparaty o podobnych właściwościach jak odrdzewiacz i podkład bazują na żywicach epoksydowych. Mają na celu przygotowanie powierzchni pod jej pomalowanie. Polecane są jako dodatkowa ochrona metali przed korozją. Gruntowanie i stosowanie podkładu antykorozyjnego na powierzchni polecane jest wtedy, gdy jest ona głęboko skorodowana, była poddana piaskowaniu lub szybkość korozji elektrochemicznej jest duża. Podkład poprawia też estetykę powierzchni, ponieważ może ją wygładzić i pomóc w zmianie koloru powierzchni. Często podkłady oferowane są w puszkach i przeznaczone są do malowania pędzlami, wałkami, jako natrysk.
![korozja Korozja: rodzaje korozji, ochrona przed korozją [krok po kroku]](https://www.mgprojekt.com.pl/blog/wp-content/uploads/2024/05/piaskowanie-rdzy.jpg)
Farba wielofunkcyjna na rdzę
Na szczególną uwagę zasługują farby wielofunkcyjne, na przykład 3 w 1, które łączą w sobie działanie kilku produktów – gruntu, farby podkładowej oraz nawierzchniowej. Można stosować je bezpośrednio na rdzę, dlatego nie ma potrzeby jej usuwania. Takie farby są często używane do prac domowych, ponieważ oszczędzają czas, a także zapewniają skuteczną ochronę przed korozją na lata. Do wyboru jest szeroka gama kolorów farb na metal, więc jednocześnie mogą one spełniać funkcję dekoracyjną.
Stosowanie preparatów zabezpieczających przed rdzą
Samodzielne używanie preparatów na rdzę nie jest skomplikowane i powłoki ochronne można wykonać samodzielnie. O czym trzeba pamiętać przed użyciem preparatów zabezpieczających przed korozją?
- Przygotowanie powierzchni. Aby powłoka była trwała i skutecznie chroniła przed rdzą, należy odpowiednią przygotować podłoże, które ma być pomalowane. Zaleca się, aby podłoże było: suche; wolne od zanieczyszczeń – pyłów, kurzu, zatłuszczeń, luźnej rdzy, resztek farby; zagruntowane i pokryte podkładem – gdy jest to konieczne. Gdy na powierzchni znajdują się stare powłoki i rdza, należy je usunąć z użyciem szczotki drucianej lub papieru ściennego, a potem odpylić. Powierzchnia powinna być zmatowiona, co powoduje lepsze przyleganie nowych warstw.
- Metody malowania. Do malowania powierzchni metalowych w celu ochrony przed rdzą można zastosować poniższe narzędzia: pędzel, wałek, urządzenia natryskowe – natrysk pneumatyczny i hydrodynamiczny. Najbardziej estetyczny efekt daje malowanie natryskowe. Wałek może natomiast zostawić po sobie charakterystyczną fakturę – aby ją zminimalizować, poleca się rozcieńczyć farbę przed nałożeniem na powierzchnię.
- Środki ostrożności. Należy pamiętać o tym, że środki stosowane na metal do ochrony antykorozyjnej mogą być niebezpieczne dla zdrowia, dlatego przy ich aplikowaniu na powierzchnię należy zachować środki ostrożności. Zaleca się stosowanie środków ochrony indywidualnej – rękawiczek oraz okularów ochronnych, ponieważ zawarte w preparatach składniki mogą działać drażniąco na skórę i oczy. Farby są również łatwopalne, dlatego należy używać ich i przechowywać je z dala od źródeł ognia i ciepła.
- Warunki malowania. Aby prace malarskie były skuteczne, należy prowadzić je w temperaturze otoczenia od 10 do 25 °C, przy temperaturze podłoża od 5 do 40 °C. Wilgotność powietrza podczas malowania powinna wynosić do 80%. Nie należy malować podczas deszczu i wtedy, gdy występuje prawdopodobieństwo opadów. Malowanie w wysokich temperaturach, podczas upałów, przy bezpośrednim nasłonecznieniu prowadzi do szybszego wysychania powłok. Może pogarszać to ich właściwości – jednorodność, trwałość.
Koszt zakupu preparatów na rdzę nie jest wysoki i można kupić je obecnie w wielu sklepach – popularnych marketach i mniejszych sklepach budowlano-wykończeniowych, sklepach metalowych. Dostępne są także przez internet.
Ceny wybranych preparatów na rdzę:
- Odrdzewiacz do żelaza w płynie (0,5 l) – 10 zł,
- Neutralizator rdzy w sprayu (0,15 l) – 25 zł,
- Farba antykorozyjna alkidowo-akrylowa (0,25 l) – 15-20 zł,
- Farba antykorozyjna alkidowo-akrylowa (2,5 l) – 100-120 zł,
- Farba antykorozyjna 3 w 1 do stosowania bezpośrednio na rdzę (5 l) – 200-220 zł,
- Podkład antykorozyjny (0,75 l) – 35 zł,
- Emalia grzejnikowa antykorozyjna w sprayu (0,4 l) – 25 zł.
Jak usunąć korozję z metalu krok po krok
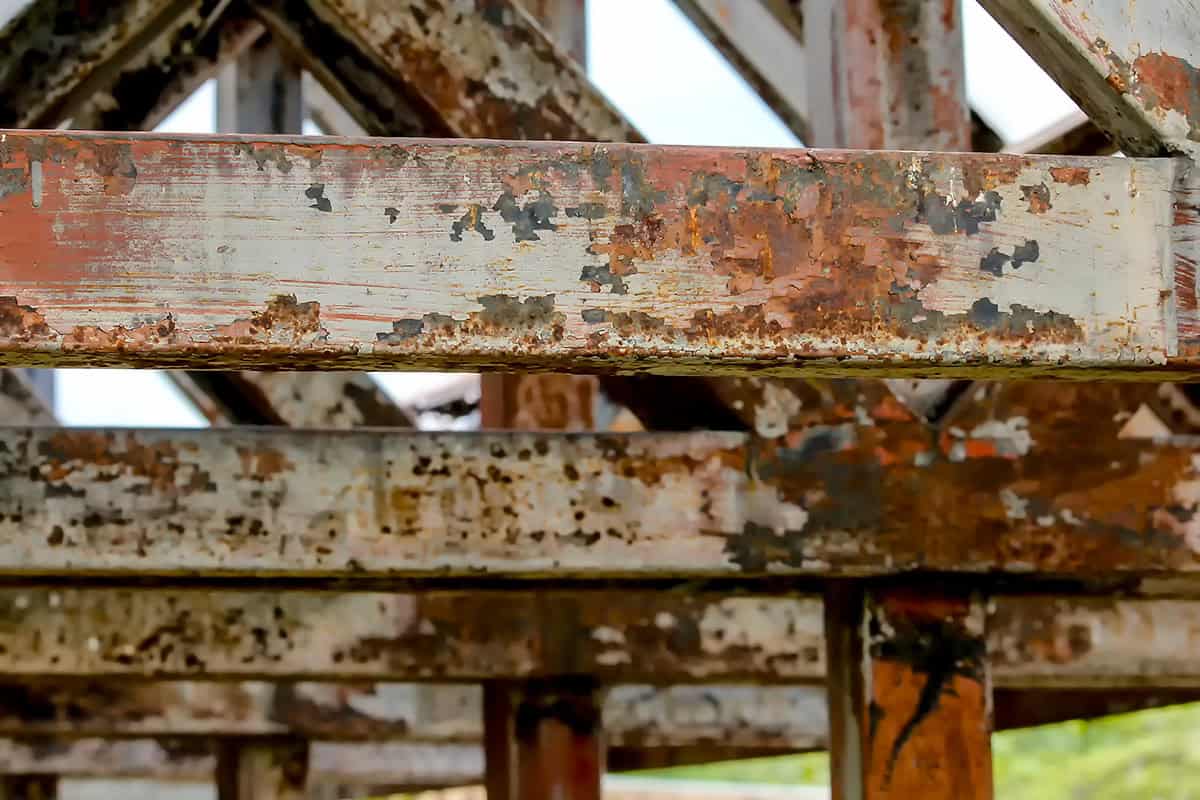
Aby usunąć rdzę z metalu i zabezpieczyć go przed ponownym korodowaniem, konieczne jest zastosowanie kilku następujących po sobie kroków:
- Przygotowanie podłoża,
- Przygotowanie materiałów,
- Gruntowanie i malowanie farbą podkładową,
- Malowanie materiałów konstrukcyjnych farbą antykorozyjną.
Dokładne informacje o ich stosowaniu można znaleźć w instrukcjach dołączonych do preparatów.
Poniżej prezentujemy, w jaki sposób należy prawidłowo usunąć rdzę z różnych zardzewiałych przedmiotów i konstrukcji, a także jak powinna wyglądać ochrona metali przed dalszą korozją:
- Przygotowanie podłoża. Przygotowanie podłoża różnych materiałów jest bardzo ważnym etapem i jego brak może zniweczyć efekty ochrony antykorozyjnej. Jeżeli na podłożu metali znajduje się widoczna rdza, w takim przypadku należy ją usunąć. Do tego celu często używane są szczotki druciane albo papier ścierny. Dla lepszych efektów można zastosować odrdzewiacz. Jeżeli rdzy towarzyszy także stara farba, która się odspaja, również należy ją usunąć. Następnie należy zmatowić powierzchnię materiałów papierem ściernym i odpylić. Gdy na powierzchni metali widoczne są zatłuszczenia, także należy je usunąć, na przykład za pomocą detergentu jak płyn do mycia naczyń lub specjalistycznego rozpuszczalnika.
- Przygotowanie wyrobów. Kolejnym krokiem jest odpowiednie przygotowanie materiałów do prac – gruntu, farby podkładowej, farby antykorozyjnej. Przed rozpoczęciem malowania metali preparat musi być dokładnie wymieszany. W trakcie prowadzenia robót należy mieszać go co godzinę. Jeżeli kupuje się kilka opakowań tej samej kolorowej farby antykorozyjnej, zaleca się wymieszać je ze sobą, aby zniwelować ewentualne różnice kolorystyczne. Gdy preparat jest zbyt gęsty, zaleca się dodanie rozcieńczalnika zalecanego przez producenta.
- Gruntowanie i malowanie farbą podkładową. Jeżeli jest to konieczne, malowanie farbą antykorozyjną zaleca się poprzedzić przez nałożenie gruntu oraz podkładu. Grunt poprawia przyczepność, a podkład pozwala na uzyskanie gładkiej i jednolitej powierzchni o wysokiej odporności na czynniki zewnętrzne. Zależnie od potrzeb można zastosować sam grunt albo samą farbę podkładową. Grunt polecany jest w przypadku każdego typu podłoża, natomiast farba podkładowa wtedy, gdy chce się wygładzić powierzchnię, zmienić jej kolor na zupełnie inny, na przykład z ciemnego na jasny. Wybierając farbę 3 w 1, nie trzeba stosować dodatkowych preparatów. W farbie zawarte są już wszystkie składniki potrzebne do malowania, co oszczędza czas.
- Malowanie farbą antykorozyjną. Prace malarskie prowadzić miękkim i płaskim pędzlem, wałkiem lub metodą natryskową w odpowiednich warunkach atmosferycznych. Malowanie powinno odbywać się metodą „mokro na mokro”, co zapobiega powstawaniu plam. Farbę należy nakładać cienką warstwą ruchami poziomymi lub pionowymi albo ruchem krzyżowym. Zalecana liczba warstw to 2-3 zależnie od preparatu. Czas potrzebny do całkowitego utwardzenia powłoki to zwykle 7 dni.
Błędy popełniane podczas malowania antykorozyjnego metali
Aby metale były skutecznie zabezpieczone przed korozją, kluczowe znaczenie ma przestrzeganie odpowiednich zasad. Jakie błędy są popełniane podczas zabezpieczania metalu przed korozją elektrochemiczną?
Sposoby zapobiegania rdzy – główne błędy:
- Nieprawidłowy dobór środka do ochrony.
- Brak przygotowana podłoża albo jego nieprawidłowe przygotowanie.
- Brak zastosowania gruntu i podkładu, gdy jest to konieczne, na przykład na mocno skorodowaną powierzchnię.
- Nieprzestrzeganie zaleceń producenta środków na rdzę, na przykład pod względem warunków aplikacji, mieszania, rozcieńczania.
- Niestaranna aplikacja, która prowadzi do powstania niewłaściwej grubości powłoki, przerw w powłoce.
Co to jest proces Sendzimira?
Proces Sendzimira to technika, w której przedmiot zanurzany jest w kąpieli cynkowej, czyli w płynnym cynku w temperaturze około 440-460 °C. Dochodzi wtedy do wytworzenia warstwy cynku, która ma postać stopu cynku i żelaza.
Jakie farby stosowane są na rdzę?
Farby stosowane na rdzę to farby akrylowe, chlorokauczukowe, alkidowe, poliuretanowe, uretanowe, poliwinylowe, alkidowo-akrylowe i alkidowo-uretanowe.
Co wpływa na szybkość korozji elektrochemicznej?
Czynniki inicjujące lub wpływające na prędkość postępowania korozji elektrochemicznej to m.in. działanie bakterii i grzybów, kruchość wodorowa oraz działania fizyczne.