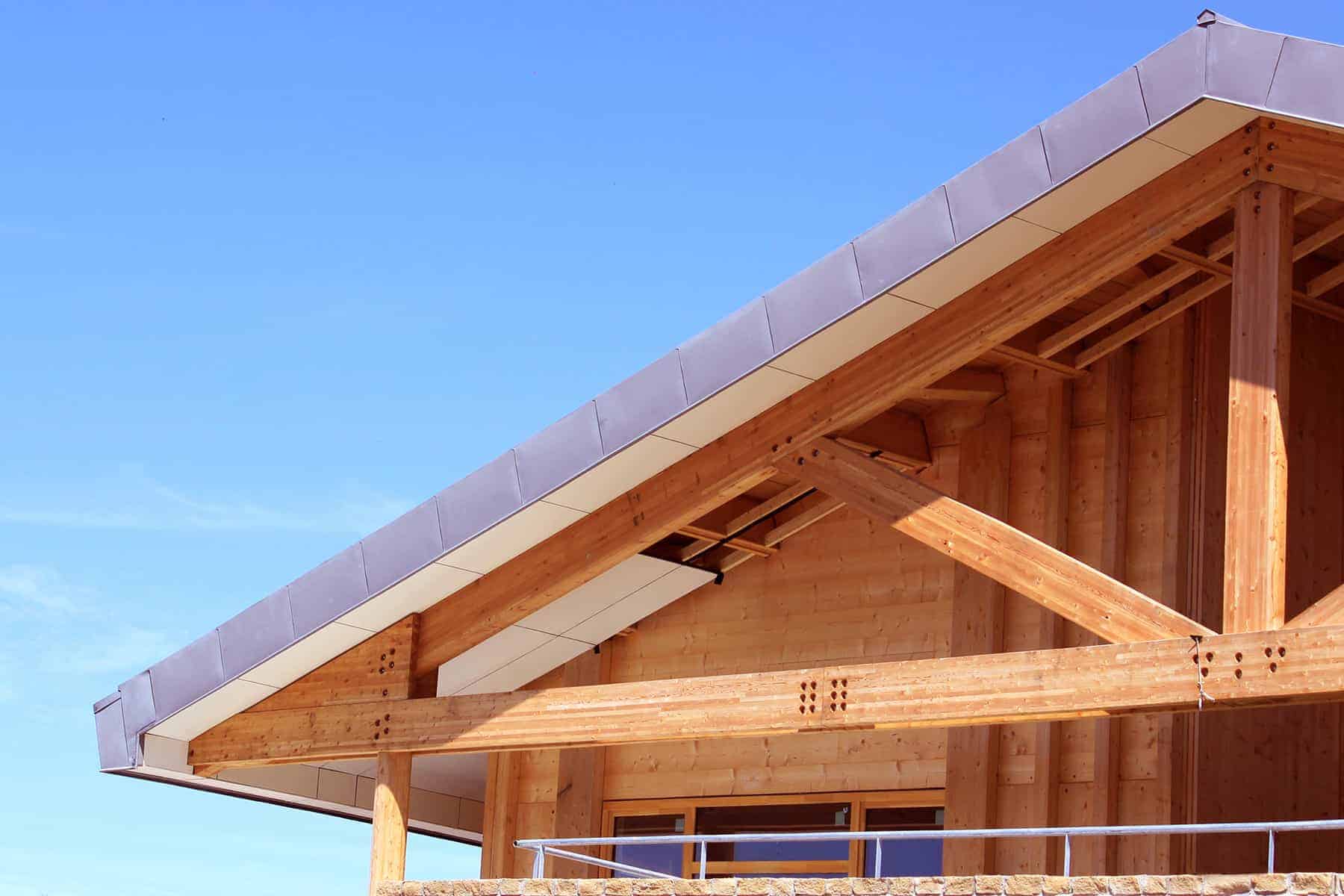
Opracowanie niezwykle trwałych klejów przyczyniło się niezawodnie do gwałtownego rozwoju nowych materiałów budowlanych. Jednym z najmłodszych i najbardziej obiecujących produktów na rynku jest drewno klejone warstwowo, nazywane również klejonką. Odpowiednio przygotowana i użytkowana klejonka ma szerokie zastosowanie i jest jest materiałem o znakomitej wytrzymałości i trwałości. Dlaczego warto rozważyć wykorzystanie drewna klejonego w nowoczesnych budownictwie mieszkaniowym? Na to pytanie postaramy się odpowiedzieć w naszym artykule.
Drewno klejone jako nowoczesny materiał budowlany
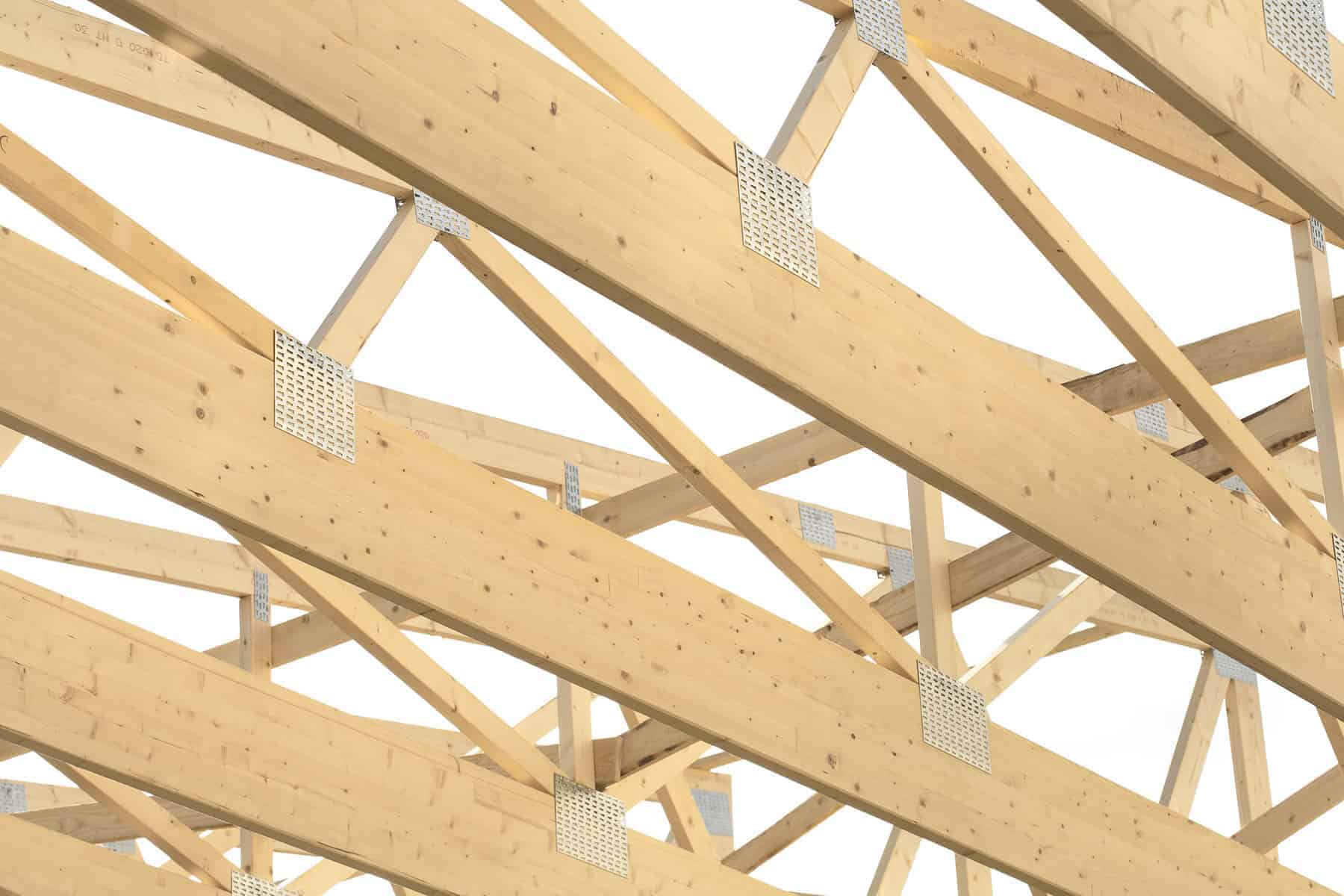
Drewno klejone bsh to nowoczesny materiał wytwarzany poprzez sklejanie ze sobą kilku warstw cienkich desek wykonanych z wysokiej jakości surowca. Drewno klejone bsh ma szerokie zastosowanie, ponieważ spełnia wysokie wymagania i znajduje wiele specjalistycznych zastosowań budowlanych. Wykorzystuje się je, między innymi w konstrukcjach nośnych, słupów, dźwigarów i masztów, a nawet przy budowie mostów.
Wśród mniej wymagających zastosowań wymienić możemy natomiast produkcję drewnianych okien czy różnego rodzaju blatów. Dzięki zastosowaniu cienkich, giętkich lameli, drewno klejone bsh charakteryzuje się wysoką plastycznością. Właściwość ta pozwala na bezproblemowe kształtowanie materiału do dowolnych form, w tym – szczególnie wymagających łuków. Z drewna klejonego powstają więc niezwykle wytrzymałe konstrukcje nośne, które można wykorzystać jako drewno konstrukcyjne klejone, ponieważ z łatwością przenoszące obciążenia w kierunku fundamentów.
Stosowanie drewna klejonego pozwala zmniejszyć zużycie materiału (a tym samym koszty budowy), zapewniając przy tym najwyższy poziom bezpieczeństwa konstrukcji.
Drewno klejone bsh pozwala także na swobodne dopasowywanie wymiarów materiału do konkretnych wymagań konstrukcyjnych. Możliwość zmiany przekrojów poprzecznych wzdłuż elementów sprawdza się znakomicie, między innymi przy budowie dachów. Aby wykorzystać materiał jako drewno konstrukcyjne deski wykorzystywane do produkcji podlegają ścisłej kontroli jakościowej. Wszystko po to, by gotowy materiał posiadał, niezbędne w konstrukcjach nośnych, ujednolicone parametry wytrzymałościowe oraz wilgotnościowe. Dzięki temu, producentom udaje się osiągnąć wytrzymałość, jakiej nie dorówna żaden rodzaj drewna litego. Mimo opisanych wyże właściwości, drewno klejone bsh jest materiałem o stosunkowo niewielkim ciężarze. Dzięki temu, nadaje się ono znakomicie do budowy obiektów, charakteryzujących się rozległymi, jednoprzestrzennymi powierzchniami (magazynów, budynków przemysłowych, budynków użyteczności publicznej, etc.). Brak konieczności stosowania podpór sprawia, że wnętrza takich obiektów są znacznie bardziej funkcjonalne, a przy tym lekkie i przestrzenne. Montaż elementów odbywa się zwykle przy wykorzystaniu klasycznych dźwigów. Niewielki ciężar materiału pozwala więc zaoszczędzić na wynajmie ciężkich maszyn budowlanych oraz na transporcie prefabrykatów na miejsce budowy.
Klejone drewno konstrukcyjne, podobnie jak surowiec, z którego zostało wykonane, jest samo w sobie materiałem o dużej trwałości. Dzięki zastosowaniu specjalnych mas klejowych, jego odporność na wodę i niesprzyjające warunki atmosferyczne jest jeszcze większa. Drewno klejone bsh bez dodatkowego impregnowania może być wykorzystywane w różnego rodzaju obiektach sportowych, a nawet na basenach. Dzięki powierzchniowym zabezpieczeniom, drewno konstrukcyjne jest stosowane w konstrukcjach nośnych narażonych na bezpośredni wpływ czynników atmosferycznych.
Estetyczne belki wykonane z klejonki posiadają także odporność na działanie płomieni, zapewniając doskonałą stabilność pod obciążeniem ogniowym. Do najważniejszych właściwości drewna klejonego należy także bardzo niski współczynnik przewodzenia ciepła. Drewno klejone bsh sprawdza się więc znakomicie zarówno przy niskich, jak i wysokich temperaturach, zapewniając optymalny komfort cieplny w pomieszczeniach.
Wytwarzanie klejonki oraz łączenie poszczególnych jej elementów na placu budowy nie stanowi najmniejszego problemu. Dlatego też, drewno klejone bsh jest chętnie wykorzystywane do produkcji konstrukcji prefabrykowanych, takich jak wiązary dachowe. W razie potrzeby, można je obrabiać przy użyciu podstawowych narzędzi ręcznych. Montaż poszczególnych elementów może być prowadzony niezależnie od pogody – nawet zimą.
Mówiąc o drewnie klejonym, nie sposób nie wspomnieć o jego niezwykłych walorach estetycznych. Pozwala ono bowiem na stworzenie unikalnego, przyjaznego klimatu, sprzyjającego zarówno pracy, jak i wypoczynkowi. Wnętrza wykończone klejonką są ciepłe, przytulne i komfortowe.
Drewno klejone warstwowo – surowce i materiały do produkcji
Do konstrukcji wykonanych z klejonki stosuje się głównie drewno świerkowe. Posiada ono bowiem nie tylko znakomite parametry wytrzymałościowe, ale także niezwykle efektowny, estetyczny wygląd. Surowiec świerkowy charakteryzuje się również dobrą odpornością na wilgoć oraz optymalną stabilnością w przypadku zmian wilgotności powietrza. Nie jest on jednak podatny na impregnację. Dlatego też, w przypadku konstrukcji wymagających dodatkowego zabezpieczenia, lepszym wyborem będzie drewno sosnowe. Impregnowanie desek pod ciśnieniem wydłuża nieco proces produkcji. Po zakończeniu impregnacji, drewno konstrukcyjne musi bowiem schnąć do czasu aż wyrówna swoją wilgotność we wszystkich przekrojach.
W przypadku bezpośredniego narażenia klejonki na wpływ opadów atmosferycznych, zaleca się natomiast stosowanie drewna modrzewiowego. Należy jednak pamiętać, że pod względem rynkowej dostępności, drewno świerkowe nie ma sobie równych. Decydując się na zastosowanie sosny, modrzewia czy jodły, trzeba więc liczyć się ze znacznie dłuższym czasem oczekiwania na gotową klejonkę. W produkcji wykorzystuje się najczęściej klej melaminowy, znacznie rzadziej – klej rezorcynowy.
Po utwardzeniu, masa klejowa oraz połączone nią drewno bsh cechują się taką samą odpornością na warunki atmosferyczne, wilgoć, ogień oraz gnicie. Kleje stosowane w produkcji drewna klejonego bsh nie wydzielają żadnych szkodliwych substancji, są więc w pełni bezpieczne, nawet w podczas kontaktu z ogniem. Warto pamiętać, że od zastosowanego kleju zależy także kolor fugi. Fugi z kleju melaminowego są szare, podczas gdy te, wykonane z kleju rezorcynowego charakteryzując się charakterystycznym czerwonobrązowym odcieniem.
Proces produkcji drewna klejonego warstwowo
Pozyskana tarcica podlega suszeniu w specjalnie do tego celu przygotowanych suszarniach. Proces ten prowadzony jest aż do uzyskania pożądanego poziomu wilgotności drewna, czyli 12% (+/- 2%). Co ważne, wilgotność poszczególnych lameli powinna być jednorodna we wszystkich przekrojach. Po wysuszeniu oraz po okresie magazynowania w magazynie drewna suchego, tarcica jest strugana do odpowiedniej grubości oraz sortowana według wymagań obowiązującej normy.
Kolejnym etapem produkcji jest usunięcie ewentualnych wad drewna oraz czyszczenie gotowych desek. Usuwa się zarówno te wady, które obniżają wytrzymałość desek, jak i te, które mają wpływ jedynie na aspekt wizualny gotowego produktu. Wykrywanie wad odbywa się w sposób w pełni zautomatyzowany przy użyciu podczerwieni oraz promieniowania X. Zidentyfikowane maszynowo miejsca są następnie oznaczane i wycinane. Przygotowane w ten sposób deski mogą zostać połączone we wstęgi. W tym celu czoła desek zostają odpowiednio wyfrezowane, tworząc tak zwane złącza palczaste, na które następnie nakładany jest klej. Kolejne deski są ze sobą ściskane, tworząc długie listwy (najczęściej o długości 20-24 m). Przed przejściem do kolejnego etapu, wstęgi (lamele) są odstawiane do całkowitego wyschnięcia kleju w złączach. Trwale połączone ze sobą deski są następnie strugane do pożądanej grubości (zazwyczaj w przedziale 15-40 mm). Grubość lameli ustala się w zależności od konkretnych zastosowań i planowanych właściwości gotowych elementów. Dla przykładu, niewielkie promienie gięcia (na poziomie około 2,5 m) pozwalają uzyskać bardzo cienkie lamele, pozwalające się wyginać do dowolnych kształtów. Na powierzchnię tak przygotowanych lameli nakładany jest klej.
Warto w tym miejscu zaznaczyć, że zawartość kleju w gotowej klejonce wynosi poniżej 1%. Kolejne warstwy układa się w specjalistycznej prasie, naginając je równocześnie do założonego kształtu. Podczas schnięcia, deski muszą pozostać ściśnięte w temperaturze co najmniej 40°C. Warunki te pozwolą bowiem na uzyskanie trwałego, wytrzymałego i odpornego złącza. Równocześnie, dla ochrony przed nadmiernym wysuszeniem materiału, należy zadbać o utrzymanie prawidłowej wilgotności powietrza. Po upływie czasu niezbędnego do utwardzenia się kleju, otrzymujemy gotową klejonkę o nadanym wcześniej kształcie. Uzyskany materiał należy poddać końcowej obróbce mechanicznej, odpowiednio dociąć końce elementów, w razie potrzeby wykonać niezbędne otwory i wcięcia, dokonać niezbędnej konserwacji powierzchni, nałożyć okucia, etc. Gotowe drewno klejone warstwowo pakowane jest w folię i transportowane na miejsce przeznaczenia. Niezwykle ważnym elementem produkcji jest kontrola w zakresie wilgotności tarcicy, wytrzymałości utworzonych złącz palczastych, jakości szlifowania uzyskanych desek, mieszania i nakładania kleju, czasu klejenia oraz warunków jego schnięcia (temperatury i wilgotności powietrza), stopnia nacisku pod prasą, etc.
Drewno klejone warstwowo czy drewno lite: porównanie parametrów
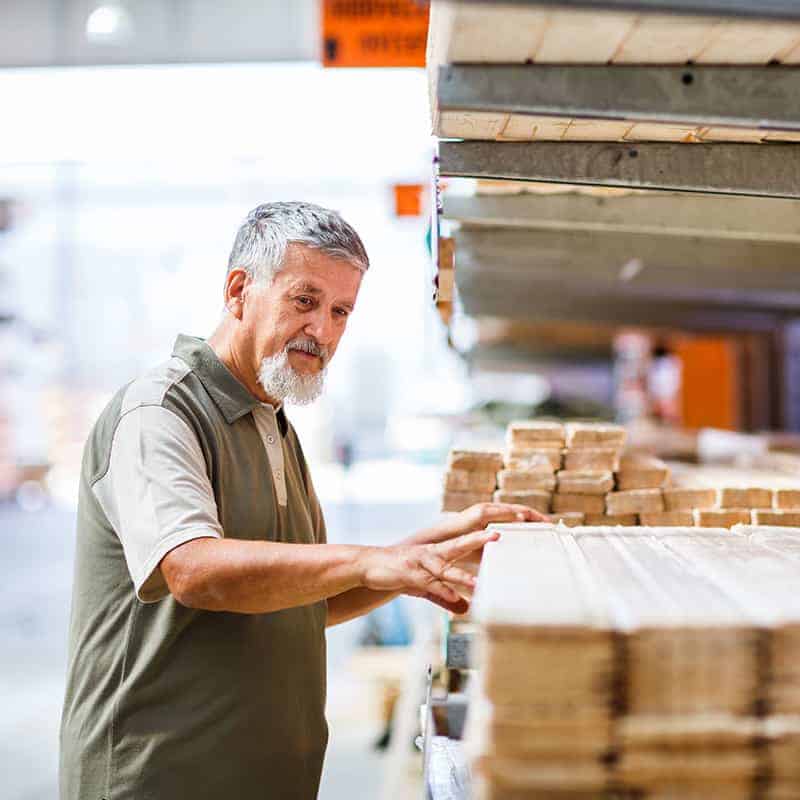
Do niedawna, drewno lite nie miało żadnej konkurencji. Wraz z pojawianiem się kolejnych odmian płyt drewnopochodnych oraz coraz bardziej popularnej klejonki, dostrzeżono, że materiały te dystansują tradycyjne drewno konstrukcyjne pod względem parametrów wytrzymałościowych, dorównując mu jednak pod względem estetycznym.
Drewno klejone bsh zapewnia lepsze właściwości mechaniczne oraz większą odporność na czynniki atmosferyczne, wilgoć czy ogień niż w przypadku drewna mokrego.
Lite drewno konstrukcyjne, ze względu na specyficzne metody produkcji, wykazuje znacznie większą podatność na różnego rodzaju uszkodzenia mechaniczne oraz czynniki biologiczne.
W porównaniu do litego drewna, klejonka jest też bardziej stabilna wymiarowo. W przeciwieństwie do drewna litego, nie wypacza się i nie kurczy, nawet pod wpływem znacznych wahań wilgotności powietrza.
Drewno klejone bsh jest także znacznie lżejsze, co ułatwia nie transport i montaż elementów na konstrukcjach nośnych, pozwalając jednocześnie na większą swobodę konstrukcyjną. Z drewna klejonego bsh budować można bowiem niezwykle efektowne obiekty o dużych rozpiętościach (bez konieczności stosowania dodatkowych podpór).
Celem powyższego zestawienia właściwości obu materiałów nie jest ocena drewna litego jako bezużytecznego do celów konstrukcyjnych, jest to bowiem materiał, którego zalety nie sposób przecenić. Warto jednak pamiętać, że do pewnych zastosowań znacznie lepiej sprawdzi się nowoczesne drewno klejone bsh.
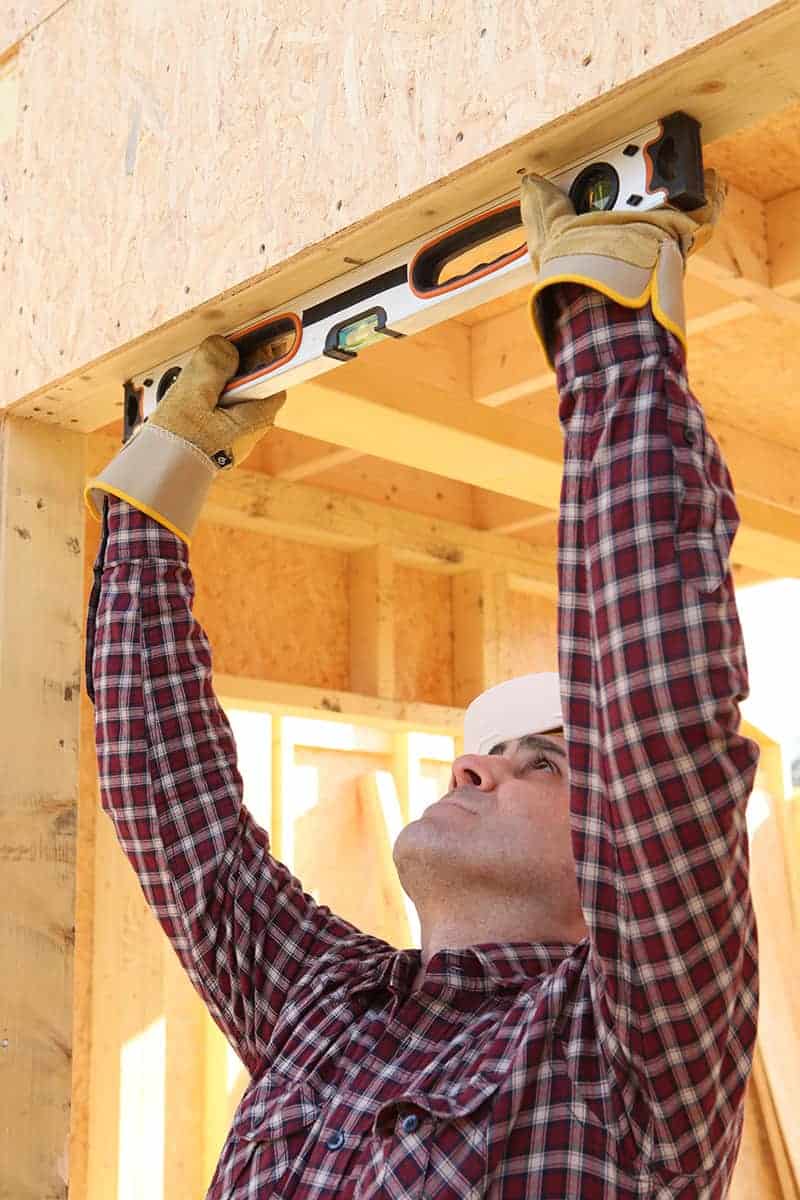
Dzięki wielu walorom, zarówno wytrzymałościowym, jak i estetycznym, drewno klejone warstwowo cieszy się coraz większą popularnością. Tendencję tą obserwować możemy od wielu lat na całym świecie.
W Polsce, ze względu na powojenny spadek zainteresowania konstrukcyjnymi zastosowaniami drewna klejonego, rozwój produkcji klejonki przebiega w nieco wolniejszym tempie.
Oto krótkie podsumowanie podstawowych zalet drewna klejonego, ważnych w budownictwie mieszkaniowym:
- Elementy wykonane z drewna klejonego bsh posiadają wysoką odporność ogniową. Zgodnie z obowiązującą klasyfikacją, klejonka o szerokości poniżej 12 cm zaliczana jest do grupy materiałów SRO (słabo rozprzestrzeniających ogień). Po impregnacji środkiem ogniochronnym lub w przypadku desek o szerokości powyżej 12 cm, klasyfikuje się ją jako NRO (nierozprzestrzeniającą ognia). Odporność ogniową (R15, R30, R60 lub R90) uzyskuje się poprzez odpowiedni sposób produkcji, bez konieczności stosowania impregnacji chemicznej. Pod wpływem ognia, zewnętrzna powłoka klejonki ulega zwęgleniu, stanowiąc warstwę ochronną dla warstw wewnętrznych, zapewniając stabilność budynku podczas pożaru. Drewno klejone warstwowo wykorzystywane jest z tego powodu w obiektach przemysłowych oraz budynkach użyteczności publicznej. Uzyskanie odporności ogniowej powyżej klasy R90 jest możliwe przy wykorzystaniu specjalnych okładzin. Rozwiązanie to jest jednak mało korzystne z estetycznego punktu widzenia. Jednocześnie ważną cechą drewna klejonego bsh stosowanego w budownictwie mieszkaniowym jest to, że jest ono mniej podatne na zmiany wilgotności.
- Drewno klejone, jako materiał wykonany z surowca naturalnego, cechuje się dobrą odpornością na działanie środowisk agresywnych. Może więc być stosowane jako drewno konstrukcyjne dachów basenów, magazynów soli oraz nawozów, etc.
- Obok doskonałych parametrów wytrzymałościowych, klejonka wyróżnia się także swoją plastycznością. Łatwa obróbka pozwala na nieomal dowolne kształtowanie materiału, ograniczając przy tym zużycie materiału oraz koszty wykonania. Konstrukcje są więc lekkie i smukłe, pełne efektownych krzywizn i atrakcyjnych łuków.
- Produkcja i montaż elementów jest łatwy i stosunkowo tani. Klejone drewno konstrukcyjne ma niewielki ciężar, co pozwala uniezależnić prace budowlane od ciężkich maszyn. Oszczędności pojawiają się także na etapie transportu klejonki.
- Istotną zaletą drewna klejonego bsh są jego walory estetyczne. Drewno klejone bsh jest tak atrakcyjne, że nie wymaga stosowania farb czy dodatkowych okładzin. Estetyczne belki przypominają lite drewno; estetyczne belki z drewna klejonego bsh nadają elewacjom oraz wnętrzom unikalny, przyjazny charakter.
Impregnacja i konserwacja
Dzięki zastosowaniu rygorystycznych norm wilgotności, drewno klejone o zastosowaniach wewnętrznych praktycznie nie wymaga żadnej dodatkowej impregnacji. Suszenie do 12% wilgotności (+/- 2%) zapewnia bowiem wystarczającą ochronę przed szkodliwym wpływem czynników biologicznych.
Dlatego też, w krajach zachodnioeuropejskich z reguły unika się stosowania dodatkowych zabezpieczeń, zgodnie z założeniem, że środki szkodliwe dla owadów czy insektów mogą w dłuższej perspektywie czasu okazać się szkodliwe także dla człowieka.
Normy polskie wymagają jednak stosowania powierzchniowej impregnacji biologicznej.
Inaczej rzecz się ma w przypadku drewna w zastosowaniach zewnętrznych – narażonego na wpływ różnego rodzaju czynników atmosferycznych. Wówczas, wykonanie odpowiedniej impregnacji jest niezbędne dla utrzymania właściwości użytkowych materiału.
Konstrukcje z drewna klejonego warstwowo
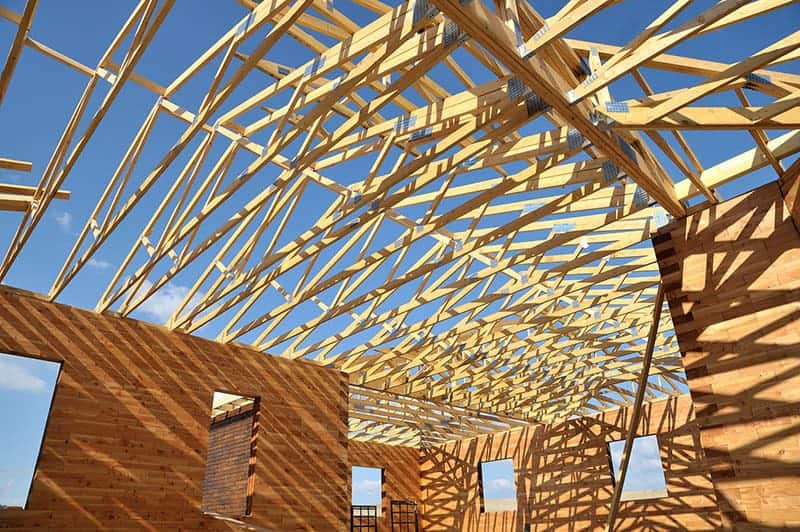
Ze względu na stosunkowo niskie koszty produkcji, transportu i montażu oraz najwyższe bezpieczeństwo użytkowania, konstrukcje z klejonki są coraz częściej stosowane w różnego rodzaju budynkach użyteczności publicznej, w tym także w obiektach sportowych, halach widowiskowych, budynkach handlowych czy biurowych.
Klejone drewno konstrukcyjne sprawdza się także znakomicie w obiektach przemysłowych. Drewno klejone warstwowo może być wykorzystywane jako jedyny materiał konstrukcyjny. Drewno klejone można również łączyć z innymi technologiami (na przykład żelbetem).
Odpowiednie przygotowanie surowca na etapie produkcyjnym pozwala na swobodne kształtowanie materiału do najbardziej kłopotliwych form – łuków i owali.
Oto kilka przykładowych konstrukcji wykonanych z klejonki:
- Dźwigar prosty o stałym przekroju, wykorzystywany w konstrukcji dachów jednospadowych. Maksymalna rozpiętość elementu (bez stosowania podpór pośrednich) może przekroczyć nawet 50 m.
- Dźwigar prosty, charakteryzujący się zmiennym przekrojem (dwutrapez), wykorzystywany w konstrukcji dachów dwuspadowych o poziomej krawędzi dolnej i spadku połaci do 5 stopni. Rozpiętość elementu może przekroczyć 50 m.
- Dźwigar gięty, charakteryzujące się zmiennym przekrojem (bumerang), wykorzystywany do konstrukcji dachów dwuspadowych o zakrzywionej krawędzi dolnej i spadku połaci do 15 stopni. Rozpiętość elementu może przekroczyć 50 m.
- Dźwigar gięty, charakteryzujący się stałym lub zmiennym przekrojem (ze ściągiem, drewnianym, stalowym lub bez niego), wykorzystywany do konstrukcji dachów łukowych.
- Dźwigar prosty, charakteryzujący się stałym lub zmiennym przekrojem (ze ściągiem drewnianym, stalowym lub bez niego), wykorzystywany w konstrukcji dachów dwuspadowych.
- Dźwigar gięty, charakteryzujący się stałym lub zmiennym przekrojem (hokej), wykorzystywany w konstrukcji dachów dwuspadowych o formie łukowej wewnątrz budynku. Konstrukcja tego typu nie zakłada żadnych ograniczeń dotyczących maksymalnego spadku połaci. Możliwe jest uzyskanie ogromnych rozpiętości.
Drewno klejone warstwowo – podział na klasy drewna
W ostatnich latach, w krajach europejskich nastąpiło niezwykle praktyczne ujednolicenie norm dla drewna warstwowego. W związku z tym, delikatnym zmianom uległ także polski podział dotyczący wytrzymałości tego materiału.
Do 2015 roku, zgodnie z normą, wyróżniano cztery klasy: GL24, GL28, GL32 oraz GL36. Aktualnie klasy jest aż siedem i są to: GL20, GL22, GL24, GL26, GL28, GL30, GL32.
Od razu widzimy więc, że obecne rozróżnienia cechują się większą subtelnością. Co więcej, z normy zniknęła klasa najwyższa – GL36. Przyczyną podjęcia takiej decyzji była praktyczna niedostępność drewna o tak wyśrubowanych parametrach.
Nawet klasa GL32 charakteryzuje się obecnie wyjątkowo niewielką dostępnością.
W opisie klas drewna możemy się spotkać ze znacznikami „C” i „H”. Znacznik „C” stosowany jest dla opisu drewna klejonego mieszanego (combined). W takich przypadkach, do produkcji klejonki wykorzystano tarcicę o różnej wytrzymałości – w warstwach zewnętrznych wytrzymałość lameli jest większa, a w osi obojętnej – mniejsza. Znacznik „H” stosujemy natomiast dla opisu drewna klejonego jednorodnego (homogeneous).
W drewnie jednorodnym w samym przekroju mamy do czynienia z lamelami o tej samej, wysokiej wytrzymałości.
Największą dostępnością na rynku cieszy się drewno klejone klasy GL24h, GL28c oraz GL30c. Wśród klas trudniej dostępnych wymienić należy: GL28h oraz GL30h. Drewno klejone klas GL32c oraz GL32h jest praktycznie niedostępne, dlatego też projektanci unikają stosowania ich w projektach domów.
W przypadku projektowania elementów wielkowymiarowych o dużych rozpiętościach, w pełni uzasadnione jest korzystanie z drewna GL28c czy GL30c. Do konstrukcjach nośnych mniej wymagających elementów w budownictwie mieszkaniowym, takich jak belki stropowe, więźby dachowe, szkielety domów drewnianych, altany czy wiaty, doskonale sprawdzi się znacznie tańsza i łatwiej dostępna klasa GL24h.
Drewno klejone warstwowo – parametry
Zgodnie z normą, każda z siedmiu wyodrębnionych klas (GL20, GL22, GL24, GL26, GL28, GL30, GL32) charakteryzuje się ściśle określonymi parametrami.
Należą do nich:
- wytrzymałość na zginanie,
- wytrzymałość na rozciąganie wzdłuż włókien,
- wytrzymałość na rozciąganie w poprzek włókien,
- wytrzymałość na ściskanie wzdłuż włókien,
- wytrzymałość na ściskanie w poprzek włókien,
- wytrzymałość na ścinanie,
- średni moduł sprężystości wzdłuż włókien,
- 5% kwantyl modułu sprężystości wzdłuż włókien,
- średni moduł sprężystości w poprzek włókien,
- 5% kwantyl modułu sprężystości w poprzek włókien,
- gęstość charakterystyczna,
- średnia gęstość.
Oznaczenie drewna | Parametry |
---|---|
Drewno konstrukcyjne GL20c | – wytrzymałość na zginanie: 20 N/mm2, – wytrzymałość na rozciąganie wzdłuż włókien: 15 N/mm2, – wytrzymałość na rozciąganie w poprzek włókien: 0,5 N/mm2, – wytrzymałość na ściskanie wzdłuż włókien: 18,5 N/mm2, – wytrzymałość na ściskanie w poprzek włókien: 2,5 N/mm2, – wytrzymałość na ścinanie: 3,5 N/mm2, – średni moduł sprężystości wzdłuż włókien: 10 400 N/mm2, – 5% kwantyl modułu sprężystości wzdłuż włókien: 8 600 N/mm2, – średni moduł sprężystości w poprzek włókien: 300 N/mm2, – 5% kwantyl modułu sprężystości w poprzek włókien: 250 N/mm2, – gęstość charakterystyczna: 355 kg/m3, – średnia gęstość: 390 kg/m3. |
Drewno konstrukcyjne GL22c | – wytrzymałość na zginanie: 22 N/mm2, – wytrzymałość na rozciąganie wzdłuż włókien: 16 N/mm2, – wytrzymałość na rozciąganie w poprzek włókien: 0,5 N/mm2, – wytrzymałość na ściskanie wzdłuż włókien: 20 N/mm2, – wytrzymałość na ściskanie w poprzek włókien: 2,5 N/mm2, – wytrzymałość na ścinanie: 3,5 N/mm2, – średni moduł sprężystości wzdłuż włókien: 10 400 N/mm2, – 5% kwantyl modułu sprężystości wzdłuż włókien: 8 600 N/mm2, – średni moduł sprężystości w poprzek włókien: 300 N/mm2, – 5% kwantyl modułu sprężystości w poprzek włókien: 250 N/mm2, – gęstość charakterystyczna: 355 kg/m3, – średnia gęstość: 390 kg/m3 |
Drewno konstrukcyjne GL24c | – wytrzymałość na zginanie: 24 N/mm2, – wytrzymałość na rozciąganie wzdłuż włókien: 17 N/mm2, – wytrzymałość na rozciąganie w poprzek włókien: 0,5 N/mm2, – wytrzymałość na ściskanie wzdłuż włókien: 21,5 N/mm2, – wytrzymałość na ściskanie w poprzek włókien: 2,5 N/mm2, – wytrzymałość na ścinanie: 3,5 N/mm2, – średni moduł sprężystości wzdłuż włókien: 11 000 N/mm2, – 5% kwantyl modułu sprężystości wzdłuż włókien: 9 100 N/mm2, – średni moduł sprężystości w poprzek włókien: 300 N/mm2, – 5% kwantyl modułu sprężystości w poprzek włókien: 250 N/mm2, – gęstość charakterystyczna: 365 kg/m3, – średnia gęstość: 400 kg/m3. |
Drewno klejone GL26c | – wytrzymałość na zginanie: 26 N/mm2, – wytrzymałość na rozciąganie wzdłuż włókien: 19 N/mm2, – wytrzymałość na rozciąganie w poprzek włókien: 0,5 N/mm2, – wytrzymałość na ściskanie wzdłuż włókien: 23,5 N/mm2, – wytrzymałość na ściskanie w poprzek włókien: 2,5 N/mm2, – wytrzymałość na ścinanie: 3,5 N/mm2, – średni moduł sprężystości wzdłuż włókien 12 000 N/mm2, – 5% kwantyl modułu sprężystości wzdłuż włókien: 10 000 N/mm2, – średni moduł sprężystości w poprzek włókien: 300 N/mm2, – 5% kwantyl modułu sprężystości w poprzek włókien: 250 N/mm2, – gęstość charakterystyczna: 385 kg/m3, – średnia gęstość: 420 kg/m3. |
Drewno klejone GL28c | – wytrzymałość na zginanie: 28 N/mm2, – wytrzymałość na rozciąganie wzdłuż włókien: 19,5 N/mm2, – wytrzymałość na rozciąganie w poprzek włókien: 0,5 N/mm2, – wytrzymałość na ściskanie wzdłuż włókien: 24 N/mm2, – wytrzymałość na ściskanie w poprzek włókien: 2,5 N/mm2, – wytrzymałość na ścinanie: 3,5 N/mm2, – średni moduł sprężystości wzdłuż włókien 12 500 N/mm2, – 5% kwantyl modułu sprężystości wzdłuż włókien: 10 400 N/mm2, – średni moduł sprężystości w poprzek włókien: 300 N/mm2, – 5% kwantyl modułu sprężystości w poprzek włókien: 250 N/mm2, – gęstość charakterystyczna: 390 kg/m3, – średnia gęstość: 420 kg/m3. |
Drewno klejone GL30c | – wytrzymałość na zginanie: 30 N/mm2, – wytrzymałość na rozciąganie wzdłuż włókien: 19,5 N/mm2, – wytrzymałość na rozciąganie w poprzek włókien: 0,5 N/mm2, – wytrzymałość na ściskanie wzdłuż włókien: 24,5 N/mm2, – wytrzymałość na ściskanie w poprzek włókien: 2,5 N/mm2, – wytrzymałość na ścinanie: 3,5 N/mm2, – średni moduł sprężystości wzdłuż włókien: 13 000 N/mm2, – 5% kwantyl modułu sprężystości wzdłuż włókien: 10 800 N/mm2, – średni moduł sprężystości w poprzek włókien: 300 N/mm2, – 5% kwantyl modułu sprężystości w poprzek włókien: 250 N/mm2, – gęstość charakterystyczna: 390 kg/m3, – średnia gęstość: 430 kg/m3. |
Drewno klejone GL32c | – wytrzymałość na zginanie: 32 N/mm2, – wytrzymałość na rozciąganie wzdłuż włókien: 19,5 N/mm2, – wytrzymałość na rozciąganie w poprzek włókien: 0,5 N/mm2, – wytrzymałość na ściskanie wzdłuż włókien: 24,5 N/mm2, – wytrzymałość na ściskanie w poprzek włókien: 2,5 N/mm2, – wytrzymałość na ścinanie: 3,5 N/mm2, – średni moduł sprężystości wzdłuż włókien: 13 500 N/mm2, – 5% kwantyl modułu sprężystości wzdłuż włókien: 11 200 N/mm2, – średni moduł sprężystości w poprzek włókien: 300 N/mm2, – 5% kwantyl modułu sprężystości w poprzek włókien: 250 N/mm2, – gęstość charakterystyczna: 400 kg/m3, – średnia gęstość: 440 kg/m3. |
Drewno klejone GL20h | – wytrzymałość na zginanie: 20 N/mm2, – wytrzymałość na rozciąganie wzdłuż włókien: 16 N/mm2, – wytrzymałość na rozciąganie w poprzek włókien: 0,5 N/mm2, – wytrzymałość na ściskanie wzdłuż włókien: 20 N/mm2, – wytrzymałość na ściskanie w poprzek włókien: 2,5 N/mm2, – wytrzymałość na ścinanie: 3,5 N/mm2, – średni moduł sprężystości wzdłuż włókien: 8 400 N/mm2, – 5% kwantyl modułu sprężystości wzdłuż włókien: 7 000 N/mm2, – średni moduł sprężystości w poprzek włókien: 300 N/mm2, – 5% kwantyl modułu sprężystości w poprzek włókien: 250 N/mm2, – gęstość charakterystyczna: 340 kg/m3, – średnia gęstość: 370 kg/m3. |
Drewno klejone GL22h | – wytrzymałość na zginanie: 22 N/mm2, – wytrzymałość na rozciąganie wzdłuż włókien: 17,6 N/mm2, – wytrzymałość na rozciąganie w poprzek włókien: 0,5 N/mm2, – wytrzymałość na ściskanie wzdłuż włókien: 22 N/mm2, – wytrzymałość na ściskanie w poprzek włókien: 2,5 N/mm2, – wytrzymałość na ścinanie: 3,5 N/mm2, – średni moduł sprężystości wzdłuż włókien: 10 500 N/mm2, – 5% kwantyl modułu sprężystości wzdłuż włókien: 8 800 N/mm2, – średni moduł sprężystości w poprzek włókien: 300 N/mm2, – 5% kwantyl modułu sprężystości w poprzek włókien: 250 N/mm2, – gęstość charakterystyczna: 370 kg/m3, – średnia gęstość: 410 kg/m3. |
Drewno klejone GL24h | – wytrzymałość na zginanie: 24 N/mm2, – wytrzymałość na rozciąganie wzdłuż włókien: 19,2 N/mm2, – wytrzymałość na rozciąganie w poprzek włókien: 0,5 N/mm2, – wytrzymałość na ściskanie wzdłuż włókien: 24 N/mm2, – wytrzymałość na ściskanie w poprzek włókien: 2,5 N/mm2, – wytrzymałość na ścinanie: 3,5 N/mm2, – średni moduł sprężystości wzdłuż włókien: 11 500 N/mm2, – 5% kwantyl modułu sprężystości wzdłuż włókien: 9 600 N/mm2, – średni moduł sprężystości w poprzek włókien: 300 N/mm2, – 5% kwantyl modułu sprężystości w poprzek włókien: 250 N/mm2, – gęstość charakterystyczna: 385 kg/m3, – średnia gęstość: 420 kg/m3. |
Drewno klejone GL26h | – wytrzymałość na zginanie: 26 N/mm2, – wytrzymałość na rozciąganie wzdłuż włókien: 20,8 N/mm2, – wytrzymałość na rozciąganie w poprzek włókien: 0,5 N/mm2, – wytrzymałość na ściskanie wzdłuż włókien: 26 N/mm2, – wytrzymałość na ściskanie w poprzek włókien: 2,5 N/mm2, – wytrzymałość na ścinanie: 3,5 N/mm2, – średni moduł sprężystości wzdłuż włókien: 12 100 N/mm2, – 5% kwantyl modułu sprężystości wzdłuż włókien: 10 100 N/mm2, – średni moduł sprężystości w poprzek włókien: 300 N/mm2, – 5% kwantyl modułu sprężystości w poprzek włókien: 250 N/mm2, – gęstość charakterystyczna: 405 kg/m3, – średnia gęstość: 445 kg/m3. |
Drewno klejone GL28h | – wytrzymałość na zginanie: 28 N/mm2, – wytrzymałość na rozciąganie wzdłuż włókien: 22,3 N/mm2, – wytrzymałość na rozciąganie w poprzek włókien: 0,5 N/mm2, – wytrzymałość na ściskanie wzdłuż włókien: 28 N/mm2, – wytrzymałość na ściskanie w poprzek włókien: 2,5 N/mm2, – wytrzymałość na ścinanie: 3,5 N/mm2, – średni moduł sprężystości wzdłuż włókien: 12 600 N/mm2, – 5% kwantyl modułu sprężystości wzdłuż włókien: 10 500 N/mm2, – średni moduł sprężystości w poprzek włókien: 300 N/mm2, – 5% kwantyl modułu sprężystości w poprzek włókien: 250 N/mm2, – gęstość charakterystyczna 425 kg/m3, – średnia gęstość: 460 kg/m3. |
Drewno klejone GL30h | – wytrzymałość na zginanie: 30 N/mm2, – wytrzymałość na rozciąganie wzdłuż włókien: 24 N/mm2, – wytrzymałość na rozciąganie w poprzek włókien: 0,5 N/mm2, – wytrzymałość na ściskanie wzdłuż włókien: 30 N/mm2, – wytrzymałość na ściskanie w poprzek włókien: 2,5 N/mm2, – wytrzymałość na ścinanie: 3,5 N/mm2, – średni moduł sprężystości wzdłuż włókien: 13 600 N/mm2, – 5% kwantyl modułu sprężystości wzdłuż włókien: 11 300 N/mm2, – średni moduł sprężystości w poprzek włókien: 300 N/mm2, – 5% kwantyl modułu sprężystości w poprzek włókien: 250 N/mm2, – gęstość charakterystyczna: 430 kg/m3, – średnia gęstość: 480 kg/m3. |
Drewno klejone GL32h | – wytrzymałość na zginanie: 32 N/mm2, – wytrzymałość na rozciąganie wzdłuż włókien: 25,6 N/mm2, – wytrzymałość na rozciąganie w poprzek włókien: 0,5 N/mm2, – wytrzymałość na ściskanie wzdłuż włókien: 32 N/mm2, – wytrzymałość na ściskanie w poprzek włókien 2,5 N/mm2, – wytrzymałość na ścinanie: 3,5 N/mm2, – średni moduł sprężystości wzdłuż włókien: 14 200 N/mm2, – 5% kwantyl modułu sprężystości wzdłuż włókien: 11 800 N/mm2, – średni moduł sprężystości w poprzek włókien: 300 N/mm2, – 5% kwantyl modułu sprężystości w poprzek włókien: 250 N/mm2, – gęstość charakterystyczna: 440 kg/m3, – średnia gęstość: 490 kg/m3. |
Ceny drewna klejonego warstwowo
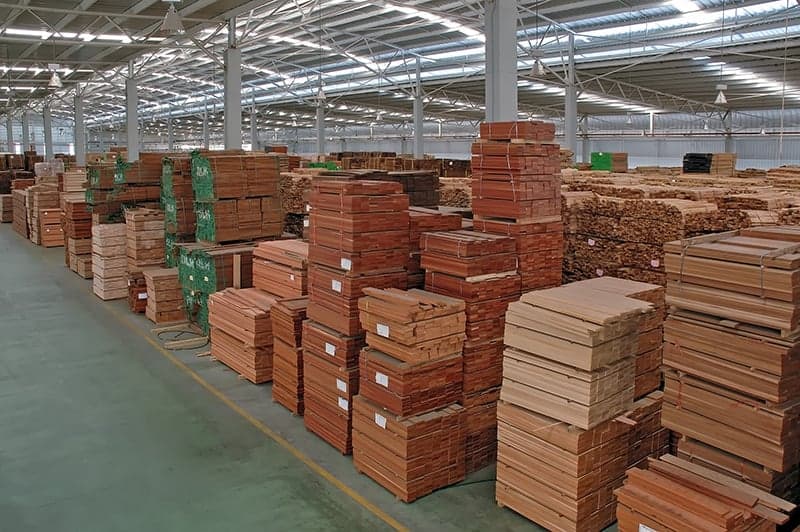
Ceny drewna klejonego warstwowo zależą od rodzaju surowca, a także grubości, długości, kształtu oraz parametrów technicznych uzyskanych lameli. Deska konstrukcyjna (drewno konstrukcyjne w klasie GL24) klejona z lameli o grubości 40 mm, wykonana z drewna świerkowego o długości 12 m, szerokości 60 cm i przekroju 12 cm to koszt około 300 zł – 350 zł. Za podobną deskę o szerokości 240 cm zapłacimy już około 2 500 zł – 2 700 zł. Cena elementów giętych jest w pełni uzależniona od konkretnych wymagań projektowych. Gotowe łuki konstrukcyjne (drewno klejone bsh w klasie GL24) wykonane z drewna świerkowego kosztują, w zależności od wymiarów oraz rodzaju wykończenia i impregnacji, 150 zł – 1600 zł.
Jaką gęstość ma drewno klejone warstwowo GL32h?
Drewno klejone warstwowo GL32h ma średnią gęstość na poziomie 490 kg/m3.
Jaką gęstość ma drewno klejone warstwowo GL28h?
Drewno klejone warstwowo GL28h ma średnią gęstość na poziomie 460 kg/m3.
Jaką gęstość ma drewno klejone warstwowo GL24h?
Drewno klejone warstwowo GL24h ma średnią gęstość na poziomie 420 kg/m3.