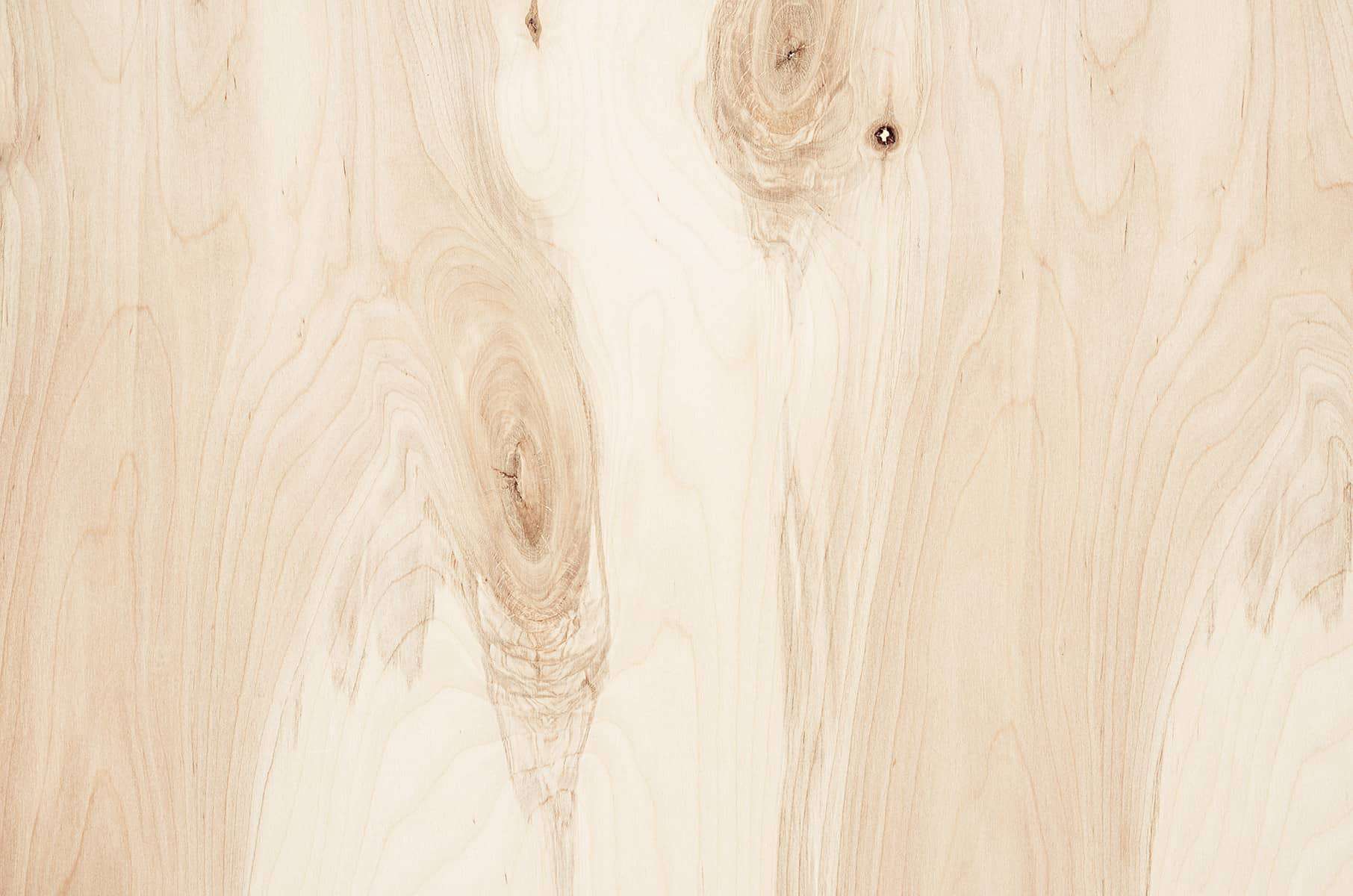
Sklejka to niezwykle zróżnicowany materiał o wszechstronnych zastosowaniach. Łatwa w produkcji, stabilna, wytrzymała oraz niezwykle efektowna, stanowi doskonałą alternatywę dla litego drewna.
Spis treści:
Sklejka drewniana – garść informacji na początek
Sklejką nazywamy płytę drewnopochodną należącą do grupy tworzyw drzewnych. Podobnie jak płyty wiórowe, stanowi ona niezwykle ciekawy przykład materiału o budowie i właściwościach odmiennych niż surowiec, z którego został on wytworzony. Zachowując najważniejsze zalety litego drewna, eliminuje ona bowiem wiele jego wad. Produkcja sklejki polega na sklejeniu nieparzystej liczby cieniutkich arkuszy drewnianych, czyli tak zwanych fornirów. Standardowa grubość pojedynczego forniru wynosi zaledwie 1,5 mm. Zewnętrzne warstwy sklejki nazywane są obłogami. Obłogi są zawsze ułożone słojami w tym samym kierunku. Warstwy wewnętrzne (środek sklejki) mogą być wykonane z tego samego lub innego (najczęściej tańszego) rodzaju drewna niż warstwy zewnętrzne. O kwalifikacji sklejki świadczy jednak zawsze rodzaj drewna, z którego wykonano obłogi. Warstwy wewnętrzne mają w tym przypadku znaczenie drugorzędne. Dlatego też, sklejka o obłogach sosnowych i olchowym środku będzie zaliczona do grupy sklejek iglastych – sosnowych. Choć najpowszechniej dostępne są sklejki zbudowane z różnych rodzajów drewna, możemy także spotkać warianty jednorodne. W szczególnych przypadkach, na przykład gdy sklejka jest przeznaczona do frezowania, jej środek może być wykonany z litego drewna. Charakterystyczną cechą sklejek są wyrównane właściwości fizyczne i mechaniczne na całej powierzchni arkusza (zarówno wzdłuż, jak i w poprzek niego). Uzyskanie takiego efektu jest możliwe dzięki charakterystycznej budowie materiału. Budowę tę nazywamy krzyżową. Otóż, każda kolejna warstwa forniru układana jest pod kątem 90 stopni w stosunku do warstwy poprzedniej. W ten sposób otrzymujemy materiał cechujący się znakomitą wytrzymałością przy stosunkowo niewielkiej grubości płyty. Mimo niezaprzeczalnych korzyści, jakie niesie ze sobą krzyżowa konstrukcja sklejek, do niektórych zastosowań najlepiej sprawdzi się materiał sklejany z fornirów ułożonych w jednym kierunku (budowa równoległa). Taka budowa gwarantuje wytrzymałość tylko w jednym, wybranym kierunku. W przeciwieństwie do litego drewna, sklejki nie pękają, nie paczą się i są łatwe w formowaniu. Dostępne w zróżnicowanych, dużych formatach, zapewniają projektantom ogromną swobodę konstrukcyjną. Sklejki, zarówno liściaste, jak i iglaste dzielą się na pięć klas jakościowych, najwyższą – E oraz klasy I-IV, z których każda kolejna dopuszcza występowanie większej ilości wad. Sklejka w klasie E nie posiada praktycznie żadnych wad. Sklejka w klasie IV to materiał, którego się nie szlifuje, a jego liczne i rozległe wady nie muszą być reperowane. Klasę tę oznacza się także symbolem CC lub określa mianem opakowaniowej. Jakość sklejki ustala się na podstawie właściwości jej prawej strony. Lewa strona płyty może się charakteryzować nieco gorszymi parametrami. Należy jednak pamiętać, że różnica jakościowa między prawą i lewą stroną sklejki nie może może przekraczać dwóch klas.
Produkcja sklejki
Proces produkcji sklejki rozpoczyna się od pozyskania odpowiednich gatunków drewna.
Do tego celu najczęściej wykorzystuje się drewno:
- sosny,
- brzozy,
- olchy,
- buka.
Pozyskany surowiec trafia do basenów warzelnianych, w których poddawany jest szczegółowo zaplanowanej obróbce hydrotermicznej. Etap ten odbywa się w temperaturze 40–60°C. Dokładne warunki kąpieli warzelnianej są dobierane w zależności od rodzaju drewna, jego średnicy oraz panującej pory roku. W przypadku drewna brzozowego, sosnowego czy świerkowego, obróbka hydrotermiczna trwa około 30 godzin. W przypadku drewna bukowego, czas ten wydłuża się nawet do 72 godzin. Obrobione hydrotermicznie drewno transportowane jest następnie do skrawarki obwodowej, gdzie zostaje poddane łuszczeniu. W wyniku łuszczenia otrzymujemy warstwy forniru w postaci długiej wstęgi. Grubość pojedynczego arkusza wynosi standardowo 1,5 mm. Możliwe jest jednak również skrawanie do innych, z góry ustalonych grubości. Uzyskane wstęgi forniru muszą zostać wysuszone. Proces ten odbywa się w suszarniach taśmowych lub rolkowych w temperaturze 160–180°C. Celem tego etapu jest zmniejszenie wilgotności forniru do ok. 4-7%. Wysuszony materiał poddawany jest kontroli jakościowej. Ewentualne wady zostają zidentyfikowane, a następnie usunięte lub naprawione. Następnie, kolejne arkusze układane są krzyżowo, krzyżowo równolegle lub równolegle względem siebie i klejone. W tym celu, odpowiednio dobrana masa klejowa nakładana jest obustronnie na co drugi arkusz forniru. Tak przygotowane forniry są w dalszej kolejności prasowane w wysokiej temperaturze i pod dużym ciśnieniem w specjalnych prasach hydraulicznych. Proces ten stanowi gwarancję trwałego połączenia arkuszy oraz doskonałych właściwości gotowego produktu. W ramach obróbki wykończeniowej, sklejki zostają docięte do pożądanych wymiarów, a ich powierzchnia zostaje skalibrowana i wygładzona na szlifierce. W zależności od przyszłych zastosowań, na sklejkę naprasowuje się specjalnie przygotowany film – papier zaimpregnowany żywicą. Na koniec, produkt jest klasyfikowany jakościowo i rozdzielany do konkretnych przeznaczeń.
Sklejka – zastosowania
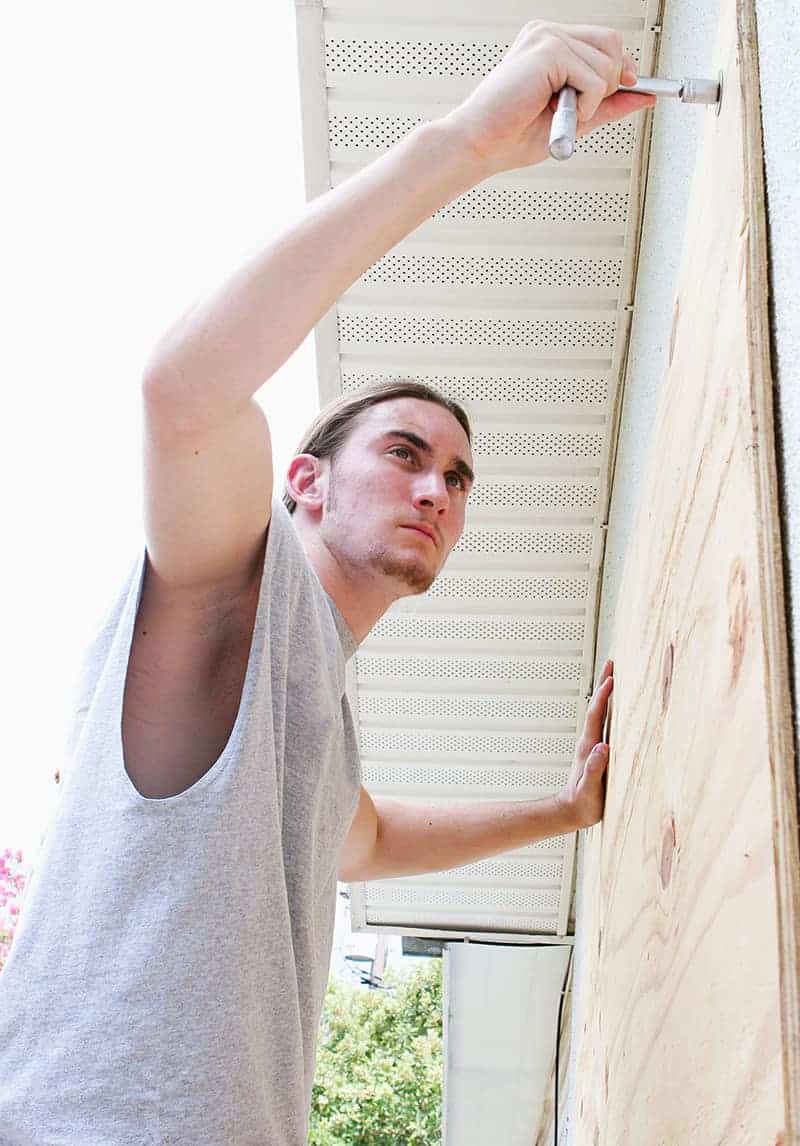
Sklejka znajduje szerokie zastosowanie w wielu gałęziach przemysłu, między innymi w przemyśle budowlanym, meblarskim, samochodowym, stoczniowym czy opakowaniowym.
Wykorzystuje się ją do budowy ścian działowych, drzwi czy poszyć dachowych.
Coraz częściej stanowi ona efektowną okładzinę ścian, podłóg czy sufitów w nowoczesnych, minimalistycznych wnętrzach.
Co więcej, specjalnie przygotowana sklejka może być stosowana również jako element zewnętrznej elewacji obiektu.
Sklejka sprawdza się znakomicie w roli wytrzymałego materiału konstrukcyjnego czy wypełniającego.
Wykorzystuje się ją w budowie deskowań czy specjalnych form do zalewania betonu.
W budynkach przemysłowych sklejka kładziona jest często na podłogi, podesty czy platformy rusztowań. Jest ona również jednym z najbardziej popularnych materiałów wykorzystywanych do produkcji wszelkiego rodzaju mebli i akcesoriów wnętrzarskich.
W przemyśle samochodowym, sklejka znajduje zastosowanie jako element konstrukcji foteli czy materiał wykończeniowy wnętrz pojazdów.
Wykorzystuje się ją również w produkcji elementów karoserii. Sklejka sprawdza się doskonale na statkach, łodziach czy jachtach.
Stosuje się ją często budowy kadłubów oraz wykończenia wnętrz różnego rodzaju jednostek pływających.
I wreszcie, sklejka to znakomity materiał opakowaniowy.
Produkuje się z niej pudełka, skrzynki oraz elementy, mające na celu chronić delikatny ładunek.
Elementy wykonane ze sklejki znajdziemy również na placach zabaw, w obudowach domowych kolumn głośnikowych, w instrumentach muzycznych, akcesoriach dekoracyjnych czy zestawach modelarskich.
Rodzaje sklejki drewnianej
Dokonując przeglądu i różnicując dostępne w sprzedaży sklejki, możemy brać pod uwagę różne ich aspekty. Od budowy, przez rodzaj zastosowanego surowca, i sposób wykończenia aż do planowanego przeznaczenia. Poniżej przedstawiamy podstawowe podziały sklejek.
- Ze względu na rodzaj drewna wykorzystany do produkcji obłogu:
- liściaste (wykonane z drewna brzozowego, olchowego, bukowego, etc.),
- iglaste (wykonane z drewna sosnowego, świerkowego, jodłowego, etc.),
- egzotyczne (wykonane z drewna meranti, ceiba, okoume, etc.).
- Ze względu na rodzaj drewna w sklejce:
- jednorodna – wykonana z drewna jednego rodzaju,
- mieszana – wykonana z kilku rodzajów drewna.
- Ze względu na rodzaj spoiny:
- suchotrwała – S (do użytku wewnętrznego) – połączona spoiną na bazie żywicy mocznikowo-formaldehydowej; przeznaczona do użytkowania w warunkach suchych,
- półwodoodporna – W1 (do użytku wewnętrznego) – połączona spoiną klejową na bazie żywicy mocznikowo-melaminowo-formaldehydowej; przeznaczona do użytkowania w warunkach wilgotnych,
- wodoodporna – W2 (do użytku zewnętrznego) – połączona spoiną na bazie żywicy fenolowo-formaldehydowej; przeznaczona do użytkowania w warunkach zewnętrznych.
- Ze względu na stopień mechanicznej obróbki płyty:
- nieszlifowana,
- szlifowana.
- Ze względu na przeznaczenie:
- przeznaczenia ogólnego – wykorzystywana powszechnie w meblarstwie oraz stolarce budowlanej,
- przeznaczenia specjalnego – między innymi: sklejki modyfikowane innymi materiałami, sklejki samolotowe, sklejki trudnopalne, etc.
Sklejki iglaste
Jednym z najbardziej popularnych rodzajów sklejek jest sklejka sosnowa.
Spośród wyrobów sosnowych, najlepszymi właściwościami odznaczają się sklejki wykonane z sosny zwyczajnej (Pinus sylvestris).
Znajdziemy je zarówno w standardowych wersjach suchotrwałych, jak i wodoodpornych.
Sklejka sosnowa posiada sosnową obłogę, podczas gdy jej środek wykonany jest najczęściej z łuszczki olchowej lub brzozowej.
W zależności od potrzeb, możemy również zdecydować się na płytę wykonaną w całości z drewna sosnowego, a nawet taką, której środek stanowi lite drewno.
Dużą popularnością cieszy się także sklejka Radiata wykonywana z drewna sosny kalifornijskiej (Pinus radiata).
Powszechnie uznaje się ją za doskonały materiał boazeryjny i elewacyjny.
Elewacje wykonane ze sklejki tego rodzaju charakteryzują się doskonałymi parametrami wytrzymałościowymi oraz niepodważalnymi walorami estetycznymi.
Innym rodzajem sklejki sosnowej jest sklejka Elliotis wykonywana z drewna sosny Elliotta (Pinus elliottii).
Typ ten charakteryzuje się poślednią jakością i znajduje zastosowanie przede wszystkim w obszarach, które nie wymagają sklejki o dużej wytrzymałości i walorach estetycznych.
Używa się ją więc głównie w produkcji opakowań.
Sklejka Elliotis występuje tylko w III i IV klasie jakości.
Posiada ona duże słoje, liczne i rozległe wady, a jej wytrzymałość na zginanie jest połowę mniejsza niż w przypadku płyt wykonanych z drewna sosny zwyczajnej. Jej niezaprzeczalną zaletą jest jednak niska cena.
Sklejki liściaste
Do najpopularniejszych sklejek liściastych na polskim rynku należą płyty olchowo-brzozowe, brzozowe oraz bukowe.
Sklejka liściasta znajduje szerokie zastosowanie w stolarstwie, meblarstwie, budownictwie, szkutnictwie, a także w przemyśle samochodowym czy opakowaniowym.
Ze względu na swoje znakomite parametry, sklejka liściasta jest z reguły droższa od sklejki iglastej.
Dzięki krótszym włóknom jest ona łatwiejsza w obróbce.
Posiada również wyższe walory estetyczne, które sprawiają, że chętnie stosuje się ją jako wykończenie szczególnie wyeksponowanych powierzchni.
Dzięki doskonałej wytrzymałości oraz efektownemu wyglądowi, sklejki liściaste są często wykorzystywane jako materiał boazeryjny i elewacyjny.
Duże wymiary formatek pozwalają na szybkie i bezproblemowe pokrywanie dużych powierzchni przy jednoczesnej minimalizacji podziałów.
Naturalna sklejka liściasta prezentuje się znakomicie jako wykończenie nowoczesnych, minimalistycznych brył.
Sklejka na budowie domu
Sklejki o podwyższonych właściwościach znajdują powszechne zastosowanie w przemyśle budowlanym, stoczniowym, szkutniczym czy motoryzacyjnym.
Materiały o takim przeznaczeniu przechodzą specjalną obróbkę, zapewniającą im wysoką odporność na wilgoć i wodę, działanie wysokich temperatur oraz inne, niekorzystne warunki atmosferyczne.
W tym celu stosuje się preparaty transparentne (oleje, woski, bezbarwne lakiery UV) lub farby kryjące do drewna.
Sklejka może też być poddana procesom zmniejszającym jej palność.
Proces uniepalniania może być wykonany na dwa sposoby. Pierwszy z nich zakłada moczenie warstw wewnętrznych sklejki w specjalnych preparatach, jeszcze przed klejeniem i prasowaniem.
Drugi – polega na wtłaczaniu odpowiednich preparatów bezpośrednio do gotowej płyty.
Sklejki do zewnętrznych zastosowań budowlanych muszą być także zabezpieczone specjalistycznymi środkami biobójczymi.
Dzięki wyrównanej wytrzymałości mechanicznej, dużej sztywności, dogodnej rozpiętości wymiarowej oraz odpowiedniemu wykończeniu, górują one zarówno nad drewnem litym, jak i innymi rodzajami płyt drewnopochodnych.
Sklejka jest znakomitym materiałem szalunkowym.
Dzięki niej, mieszanka betonowa zyskuje pożądany kształt oraz efektowny wygląd.
W obszarze deskowań, wysoko cenione są sklejki wytworzone z drewna drzew liściastych.
Materiały takie mają dużą grubość i składają się zwykle z kilkunastu warstw.
Do szalunków stosuje się sklejki wodoodporne, zabezpieczone specjalnym filmem fenolowym.
Coraz większą popularnością na polskim rynku cieszą się także tak zwane sklejki antypoślizgowe.
Produkuje się je zarówno z drewna drzew liściastych, jak i iglastych, najczęściej spotykane są jednak połączenia liściaste – brzozowo-olchowe.
Wodoodporne sklejki antypoślizgowe wykorzystywane są do budowy lekkich i wytrzymałych podestów, rusztowań oraz platform.
Zapewniają one wysoki komfort oraz bezpieczeństwo poruszania się w wymagających warunkach, między innymi na budowach czy w halach przemysłowych.
Zalety i wady sklejki
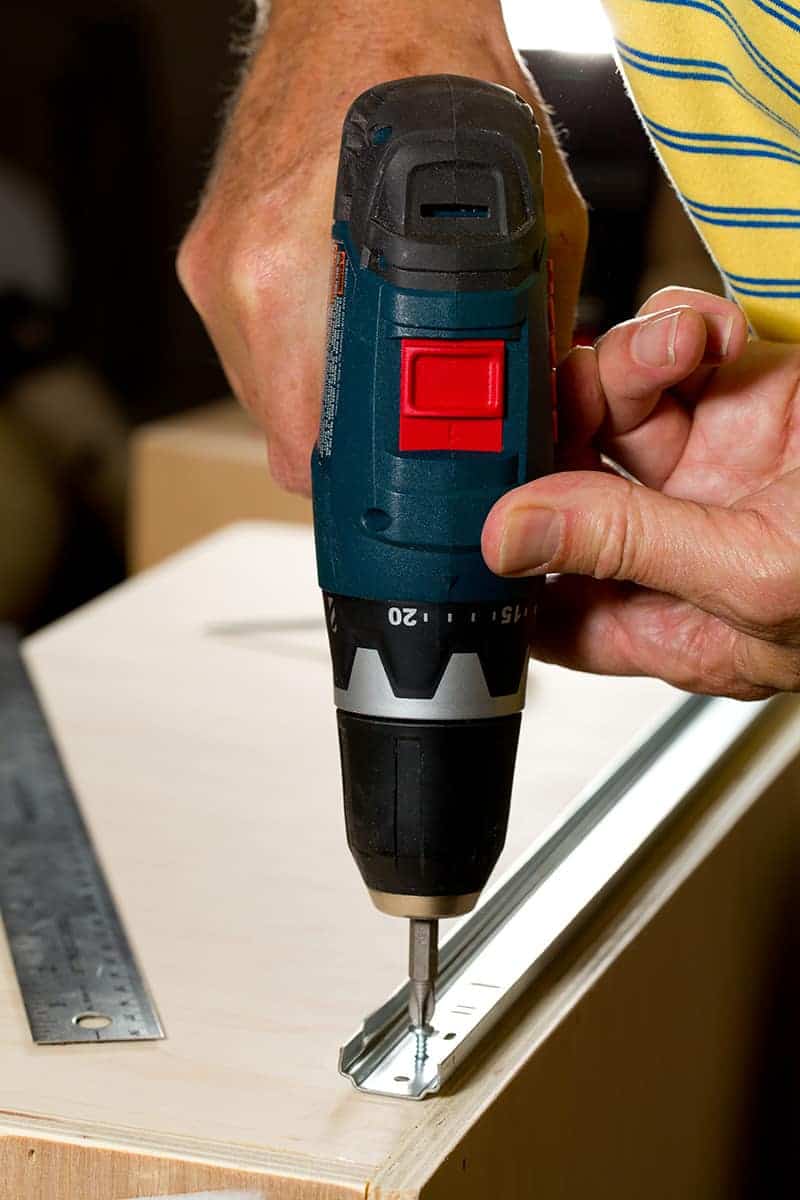
Sklejki charakteryzują się doskonałą wytrzymałością na zginanie, rozciąganie oraz ściskanie, a także wysokim modułem sprężystości.
Parametrami tymi znacznie przewyższają inne materiały drewnopochodne, a nawet lite drewno.
Co więcej, zarówno w stanie suchym, jak i mokrym, wykazują one wysoką odporność na udar.
Sklejki są bardzo cenione ze względu na swą stabilność wymiarową.
W porównaniu do innych płyt drewnopochodnych, zachodzące w sklejce procesy pęcznienia są bardzo ograniczone, a po wyschnięciu sklejka wraca do pierwotnych wymiarów.
Produkcja sklejki pozwala na bardziej korzystne, zarówno pod względem ekologicznym, jak i ekonomicznym, gospodarowanie surowcem drewnianym.
Ponadto, proces produkcji sklejki charakteryzuje się wysoką efektywnością energetyczną.
Niezbędna do produkcji energia może być bowiem niemal w całości pozyskana podczas spalania pozostałości drzewnych.
Ogromną zaletą sklejki jest także wszechstronność jej zastosowań.
Sprawdzi się zarówno w produkcji mebli, jak i deskowań, różnego rodzaju budowlanych elementów konstrukcyjnych, rusztowań przemysłowych czy opakowań.
Sklejka stosowana jako materiał boazeryjny lub elewacyjny to także dodatkowa warstwa izolacji, zarówno termicznej, jak i izolacji akustycznej.
Odpowiednio zabezpieczona, wykazuje znakomitą odporność na działanie wody oraz niekorzystnych warunków atmosferycznych
Sklejka drewniana nie posiada wielu wad.
Możemy jednak zaliczyć do nich stosunkowo wysoką cenę (w porównaniu do innych płyt drewnopochodnych) oraz bezwzględną konieczność starannego zabezpieczania materiału specjalistycznymi preparatami.
Podsumowując, do najważniejszych zalet sklejki drewnianej zaliczamy:
- wysoką wytrzymałość w porównaniu do innych płyt drewnopochodnych oraz litego drewna,
- doskonałą trwałość – przedmioty wykonane ze sklejki mogą przetrwać w dobrym stanie wiele, wiele lat,
- znakomitą wytrzymałość mechaniczną w stosunku do grubości płyty,
- odporność na czynniki zewnętrzne (sklejka, w przeciwieństwie do litego drewna, nie pęka i nie paczy się),
- łatwość formowania, w tym – gięcia,
- dobre wykorzystanie pozyskanego surowca – z tej samej ilości drewna uzyskamy więcej metrów kwadratowych sklejki niż litego drewna,
- wysoką stabilność wymiarową,
- dobrą efektywność energetyczną procesu produkcji,
- niezwykłą wszechstronność zastosowań,
- bardzo zróżnicowane wielkości dostępnych formatów,
- gładką powierzchnię, umożliwiającą bezproblemowe czyszczenie materiału.
Klasy jakości sklejki drewnianej
Jak już wspominaliśmy, sklejka drewniana jest różnicowana pod względem jakości na pięć podstawowych klas: E, I, II, III i IV. Materiał z każdej klasy jakościowej musi spełniać ściśle określone wymogi. Oto ich podsumowanie.
Sklejka liściasta
Klasa jakości E
Nie dopuszcza się praktycznie żadnych wad
Klasa jakości I
Dopuszcza się:
- sęki szpilkowe – maksymalnie 3 sztuki/m2
- sęki zdrowe zrośnięte – pojedyncze o średnicy jednostkowej do 15 mm. Suma ich średnic nie może jednak przekroczyć 30 mm/m2. W sękach mogą występować minimalne pęknięcia.
- sęki zepsute i niezrośnięte oraz otwory po sękach – o średnicy jednostkowej do 6 mm, pod warunkiem, że zostały one wypełnione; maksymalnie 2 sztuki/m2
- pęknięcia otwarte – o długości mniejszej niż 1/10 długości płyty i o szerokości jednostkowej do 3 mm, pod warunkiem, że są dobrze wypełnione; maksymalnie 3sztuki/m szerokości płyty
- pęknięcia zamknięte
- wady budowy drewna – pod warunkiem, że są one bardzo niewielkie
- przebarwienie, które nie powoduje niszczenia drewna – możliwe nieznaczne zróżnicowanie barwy
- naprawy w postaci łat, wstawek lub klinów – pod warunkiem, że zostały prawidłowo wykonane i dokładnie wypełnione; maksymalnie 3 sztuki/m2
- uszkodzenia krawędzi płyty pod wpływem szlifowania lub piłowania – pod warunkiem, że występują do 2 mm od krawędzi płyty
Nie dopuszcza się:
- uszkodzenia spowodowane przez owady, świdraka morskiego oraz rośliny pasożytnicze
- zakorek
- powodowany przez grzyby rozkład niszczący drewno
- otwarte spoiny
- zakładki
- pęcherze
- wgłębienia, odciski i wybrzuszenia
- szorstkość
- przeszlifowanie przechodzące
- przebicie klejowe
- wtrącenia ciał obcych
- naprawy w postaci wypełnienia syntetycznego
Klasa jakości II
Dopuszcza się:
- sęki szpilkowe
- sęki zdrowe zrośnięte – o średnicy jednostkowej do 35 mm. W sękach mogą wystąpić niewielkie pęknięcia.
- sęki zepsute i niezrośnięte oraz otwory po sękach – w przypadku wad nienaprawionych: o średnicy jednostkowej do 5 mm. W przypadku wad wypełnionych: o średnicy jednostkowej do 10 mm; maksymalnie 3sztuki/m2
- pęknięcia otwarte – o długości mniejszej niż 1/5 długości płyty i szerokości jednostkowej do 5 mm, pod warunkiem, że są dobrze wypełnione; maksymalnie 3sztuki/m szerokości płyty
- pęknięcia zamknięte
- uszkodzenia spowodowane przez owady oraz świdraka morskiego – o średnicy do 3 mm pionowo do płaszczyzny płyty; maksymalnie 10 sztuk/m2
- zakorek – o szerokości do 5 mm, pod warunkiem, że został poprawnie wypełniony
- wady budowy drewna – pod warunkiem, że są one niewielkie
- przebarwienie, które nie powoduje niszczenia drewna – możliwe nieznaczne zróżnicowanie barwy
- otwarte spoiny – o szerokości do 3 mm; maksymalnie 1sztuka/m szerokości płyty. Jeżeli szerokość jest większa niż 1 mm, spoiny należy wypełnić.
- zakładki – o długości do 100 mm; maksymalnie 1 sztuka/m2
- wgłębienia, odciski i wybrzuszenia – pod warunkiem, że są one niewielkie
- szorstkość – pod warunkiem, że jest ona niewielka
- przebicie klejowe – pod warunkiem, że jest niewielkie i występuje sporadycznie
- wtrącenia ciał obcych – pod warunkiem, że nie są to cząstki żelaza
- naprawy w postaci łat, wstawek lub klinów – pod warunkiem, że są prawidłowo wykonane i dokładnie wypełnione; maksymalnie 6 sztuk/m2
- naprawy w postaci wypełnienia syntetycznego – w ramach określonych granic
- uszkodzenia krawędzi płyty pod wpływem szlifowania lub piłowania – pod warunkiem, że występują do 5 mm od krawędzi płyty
Nie dopuszcza się:
- uszkodzeń spowodowanych przez rośliny pasożytnicze
- powodowanego przez grzyby rozkładu niszczącego drewno
- pęcherzy
- przeszlifowania przechodzącego
Klasa jakości III
Dopuszcza się:
- sęki szpilkowe
- sęki zdrowe zrośnięte – o średnicy jednostkowej do 50 mm
- sęki zepsute i niezrośnięte oraz otwory po sękach – o średnicy jednostkowej do 40 mm
- pęknięcia otwarte – o długości mniejszej niż 1/3 długości płyty i szerokości jednostkowej do 20 mm; maksymalnie 3sztuki/m2 szerokości płyty, jeżeli nie są naprawione; pęknięcia wypełnione – bez ograniczeń
- pęknięcia zamknięte
- uszkodzenia spowodowane przez owady oraz świdraka morskiego – o szerokości do 15 mm i długości do 60 mm; maksymalnie 3 sztuki/m2
- zakorek – o szerokości do 55 mm
- wady budowy drewna
- przebarwienie, które nie powoduje niszczenia drewna
- otwarte spoiny – o szerokości do 5 mm; maksymalnie 2 sztuki/m szerokości płyty
- zakładki – maksymalnie 2 sztuki/m2
- wgłębienia, odciski i wybrzuszenia
- szorstkość
- przeszlifowanie przechodzące – w rozmiarze do 1% powierzchni płyty
- przebicie klejowe – w rozmiarze do 5% powierzchni płyty
- wtrącenia ciał obcych – pod warunkiem, że nie są to cząstki żelaza
- naprawy w postaci łat, wstawek lub klinów – pod warunkiem, że zostały one prawidłowo wykonane i dokładnie wypełnione; liczba bez ograniczeń
- naprawy w postaci wypełnienia syntetycznego – w ramach określonych granic
- uszkodzenia krawędzi płyty pod wpływem szlifowania lub piłowania – pod warunkiem, że występują one do 5 mm od krawędzi płyty
Nie dopuszcza się:
- uszkodzeń spowodowanych przez rośliny pasożytnicze
- powodowanego przez grzyby rozkładu niszczącego drewno
- pęcherzy
Klasa jakości IV
Dopuszcza się:
- sęki szpilkowe
- sęki zdrowe zrośnięte – o ile nie pogarszają przydatności płyty
- sęki zepsute i niezrośnięte oraz otwory po sękach – o ile nie pogarszają przydatności płyty
- pęknięcia otwarte – o ile nie pogarszają przydatności płyty
- pęknięcia zamknięte
- uszkodzenia spowodowane przez owady, świdraka morskiego oraz rośliny pasożytnicze – o ile nie pogarszają przydatności płyty
- zakorek – o ile nie pogarsza przydatności płyty
- wady budowy drewna
- przebarwienie, które nie powoduje niszczenia drewna
- otwarte spoiny – o szerokości do 25 mm; liczba bez ograniczeń
- zakładki – o ile nie pogarszają przydatności płyty
- wgłębienia, odciski i wybrzuszenia
- szorstkość
- przeszlifowanie przechodzące – w rozmiarze do 5% powierzchni płyty, o ile nie pogarsza ono jej przydatności
- przebicie klejowe – o ile nie pogarsza przydatności płyty
- wtrącenia ciał obcych – pod warunkiem, że nie są to cząstki żelaza
- naprawy w postaci łat, wstawek lub klinów – pod warunkiem, że są one prawidłowo wykonane i dokładnie wypełnione; liczba bez ograniczeń
- naprawy w postaci wypełnienia syntetycznego – liczba bez ograniczeń
- uszkodzenia krawędzi płyty pod wpływem szlifowania lub piłowania – pod warunkiem, że są one prawidłowo wykonane i dokładnie wypełnione; bez ograniczeń
Nie dopuszcza się:
- powodowanego przez grzyby rozkładu niszczącego drewno
- pęcherzy
Sklejka iglasta
Klasa jakości E
Nie dopuszcza się praktycznie żadnych wad
Klasa jakości I
Dopuszcza się:
- sęki szpilkowe – maksymalnie 3 sztuki/m2
- sęki zdrowe zrośnięte – pojedyncze, do średnicy 15 mm. Ich łączna średnica nie może jednak przekroczyć 30 mm/m2. W sękach mogą występować minimalne pęknięcia.
- sęki zepsute i niezrośnięte oraz otwory po sękach – pojedyncze do średnicy 6 mm, pod warunkiem, że zostały one wypełnione; maksymalnie 2 sztuki/m2
- pęknięcia otwarte – o długości mniejszej niż 1/10 długości płyty i o szerokości jednostkowej do 3 mm, pod warunkiem, że zostaną one dobrze wypełnione; maksymalnie 3 sztuki/m
- pęknięcia zamknięte
- wady budowy drewna – o ile są bardzo niewielkie
- przebarwienie, które nie powoduje niszczenia drewna – możliwe nieznaczne zróżnicowanie barwy
- naprawy: łaty, wstawki lub kliny – pod warunkiem, że zostały prawidłowo wykonane oraz szczelnie wypełnione; maksymalnie 5 sztuk/m2
- uszkodzenia krawędzi płyty w wyniku szlifowania lub piłowania – pod warunkiem, że występują one do 2 mm od krawędzi płyty
Nie dopuszcza się:
- uszkodzeń spowodowanych przez owady, świdraka morskiego oraz rośliny pasożytnicze
- pęcherzy żywicznych i zakorków
- przeżywiczenia
- powodowanego przez grzyby rozkładu niszczącego drewno
- otwartych spoin
- zakładek
- pęcherzy
- wgłębień, odcisków oraz wybrzuszeń
- szorstkości
- przeszlifowania przechodzącego
- przebicia klejowego
- wtrąceń ciał obcych
- napraw w postaci wypełnień syntetycznych
Klasa jakości II
Dopuszcza się:
- sęki szpilkowe
- sęki zdrowe zrośnięte – do średnicy 50 mm. W sękach mogą występować niewielkie pęknięcia.
- sęki zepsute i niezrośnięte oraz otwory po sękach – do średnicy 5 mm, jeśli nie są wypełnione; do średnicy 25 mm, pod warunkiem, że zostały one wypełnione; maksymalnie 6 sztuk/m2
- pęknięcia otwarte – o długości mniejszej niż 1/3 długości płyty i o szerokości jednostkowej do 10 mm; maksymalnie 3 sztuki/m. Wszystkie pęknięcia powyżej 2 mm powinny zostać wypełnione.
- pęknięcia zamknięte
- uszkodzenia spowodowane przez owady oraz świdraka morskiego – do średnicy 3 mm pionowo do płaszczyzny płyty; maksymalnie 10 sztuk/m2
- pęcherze żywiczne i zakorek – do szerokości 6 mm, pod warunkiem, że zostaną dobrze wypełnione
- przeżywiczenie – pod warunkiem, że jest niewielkie
- wady budowy drewna – pod warunkiem, że są niewielkie
- przebarwienia, które nie powodują niszczenia drewna – możliwe nieznaczne zróżnicowanie barwy
- otwarte spoiny – do szerokości 3 mm, maksymalnie 1sztuka/m szerokości płyty; w przypadku spoin o szerokości powyżej 1 mm, należy je wypełnić.
- zakładki – do długości 10 mm; maksymalnie 1 sztuka/m2
- wgłębienia, odciski i wybrzuszenia – pod warunkiem, że są niewielkie
- szorstkość – pod warunkiem, że jest niewielka
- przebicie klejowe – pod warunkiem, że jest niewielkie i występuje sporadycznie
- wtrącenia ciał obcych – pod warunkiem, że nie są to cząstki żelaza
- naprawy w postaci łat, wstawek lub klinów – pod warunkiem, że zostały prawidłowo wykonane i dokładnie wypełnione; liczba bez ograniczeń
- naprawy w postaci wypełnienia syntetycznego – w ramach określonych granic
- uszkodzenia krawędzi płyty pod wpływem szlifowania lub piłowania – pod warunkiem, że występują do 5 mm od krawędzi płyty
Nie dopuszcza się:
- uszkodzeń spowodowanych przez rośliny pasożytnicze
- powodowanego przez grzyby rozkładu niszczącego drewno
- pęcherzy
- przeszlifowania przechodzącego
Klasa jakości III
Dopuszcza się:
- sęki szpilkowe
- sęki zdrowe zrośnięte – do średnicy jednostkowej 60 mm
- sęki zepsute i niezrośnięte oraz otwory po sękach – do średnicy jednostkowej 40 mm
- pęknięcia otwarte – o długości mniejszej niż 1/2 długości płyty i o szerokości jednostkowej do 15 mm; maksymalnie 3 sztuki/m
- pęknięcia zamknięte
- uszkodzenia spowodowane przez owady oraz świdraka morskiego – o szerokości do 15 mm i długości do 60 mm; maksymalnie 3 sztuki/m2
- pęcherze żywiczne i zakorek – do szerokości 40 mm
- przeżywiczenie
- wady budowy drewna
- przebarwienia, które nie powodują niszczenia drewna
- otwarte spoiny – w przypadku spoin niewypełnionych: do szerokości 10 mm, maksymalnie 2 sztuki/m szerokości płyty
- zakładki – maksymalnie 2 sztuki/m2
- wgłębienia, odciski i wybrzuszenia
- szorstkość
- przeszlifowanie przechodzące – w rozmiarze do 1% powierzchni płyty
- przebicie klejowe – w rozmiarze do 5% powierzchni płyty
- wtrącenia ciał obcych – pod warunkiem, że nie są to cząstki żelaza
- naprawy w postaci łat, wstawek lub klinów – pod warunkiem, że zostały prawidłowo wykonane i dokładnie wypełnione; liczba bez ograniczeń
- naprawy w postaci wypełnienia syntetycznego – w ramach określonych granic
- uszkodzenia krawędzi płyty pod wpływem szlifowania lub piłowania – pod warunkiem, że występują do 5 mm od krawędzi płyty
Nie dopuszcza się:
- uszkodzeń spowodowanych przez rośliny pasożytnicze
- powodowanego przez grzyby rozkładu niszczącego drewno
- pęcherzy
Klasa jakości IV
Dopuszcza się:
- sęki szpilkowe
- sęki zdrowe zrośnięte – o ile nie pogarszają przydatności płyty
- sęki zepsute i niezrośnięte oraz otwory po sękach – o ile nie pogarszają przydatności płyty
- pęknięcia otwarte – o ile nie pogarszają przydatności płyty
- pęknięcia zamknięte
- uszkodzenia spowodowane przez owady, świdraka morskiego oraz rośliny pasożytnicze – o ile nie pogarszają przydatności płyty
- pęcherze żywiczne i zakorek – o ile nie pogarszają przydatności płyty
- przeżywiczenie
- wady budowy drewna
- przebarwienia, które nie powodują niszczenia drewna
- otwarte spoiny – w przypadku spoin niewypełnionych: do szerokości 25 mm; ilość nieograniczona
- zakładki – maksymalnie 1 sztuka/m2 do długości 100 mm
- wgłębienia, odciski i wybrzuszenia
- szorstkość
- przeszlifowanie przechodzące – w rozmiarze do 5% powierzchni płyty, o ile nie pogarsza przydatności płyty
- przebicie klejowe – o ile nie pogarsza przydatności płyty
- wtrącenia ciał obcych – pod warunkiem, że nie są to cząstki żelaza
- naprawy w postaci łat, wstawek lub klinów – pod warunkiem, że zostały prawidłowo wykonane i dokładnie wypełnione; liczba bez ograniczeń
- naprawy w postaci wypełnienia syntetycznego – bez ograniczeń
- uszkodzenia krawędzi płyty pod wpływem szlifowania lub piłowania – bez ograniczeń, pod warunkiem, że zostały prawidłowo wykonane i dokładnie wypełnione
Nie dopuszcza się:
- powodowanego przez grzyby rozkładu niszczącego drewno
- pęcherzy
Cena sklejek drewnianych
Cena sklejki zależy przede wszystkim od jej właściwości, wymiarów, rodzaju wykończenia oraz zastosowanego do jej produkcji drewna.
Najmniej zapłacimy za sklejkę suchotrwałą – płyty o grubości 4 mm i wymiarach 1250 x 2500 mm kosztują zwykle od około 50-60 zł w górę.
Płyty wodoodporne o tej samej grubości i wymiarach to z kolei koszt co najmniej 80 zł.
W przypadku sklejek specjalnego przeznaczenia, podane wyżej ceny zwiększą się nawet kilkukrotnie.